In CNC machining, parameters are crucial for achieving high-quality results. Much like the ingredients in a recipe determine the taste and texture of a dish, machining parameters define how effectively and efficiently a CNC machine operates. Understanding and optimizing these parameters is essential for enhancing performance, prolonging tool life, and ensuring precision.
What Are CNC Machining Parameters?
CNC machining parameters are the settings that dictate how a CNC machine operates. These parameters directly affect cutting conditions, impacting performance, surface quality, tool longevity, and overall productivity. Key CNC machining parameters include cutting speed, feed rate, depth of cut, spindle speed, plunge rate, and tool path strategies.
Why Are CNC Machining Parameters So Important?
Getting CNC machining parameters right is not just a technicality—it’s essential for achieving superior results and maintaining operational efficiency. Here’s why precise parameter settings are crucial:
- Precision and Repeatability: Accurate CNC machining parameters ensure that each part meets exact specifications. Consistent settings lead to repeatable outcomes, reducing defects and ensuring high-quality production.
- Tool Longevity: Properly adjusted parameters can significantly extend the lifespan of your cutting tools. For instance, choosing the correct cutting speed and feed rate helps minimize wear and tear, reducing the need for frequent tool replacements.
- Surface Quality: Parameters such as spindle speed and feed rate impact the surface finish of your parts. Optimizing these settings ensures a smooth, high-quality finish, which is vital for both aesthetics and functionality.
- Material Efficiency: Effective parameter settings help in material removal without causing excessive waste. Correct depth of cut and feed rate ensure efficient machining without overloading the machine or damaging the workpiece.
- Cost Reduction: Optimizing parameters can lower production costs by reducing machining time and tool wear. This results in savings on labor and material costs, improving overall profitability.
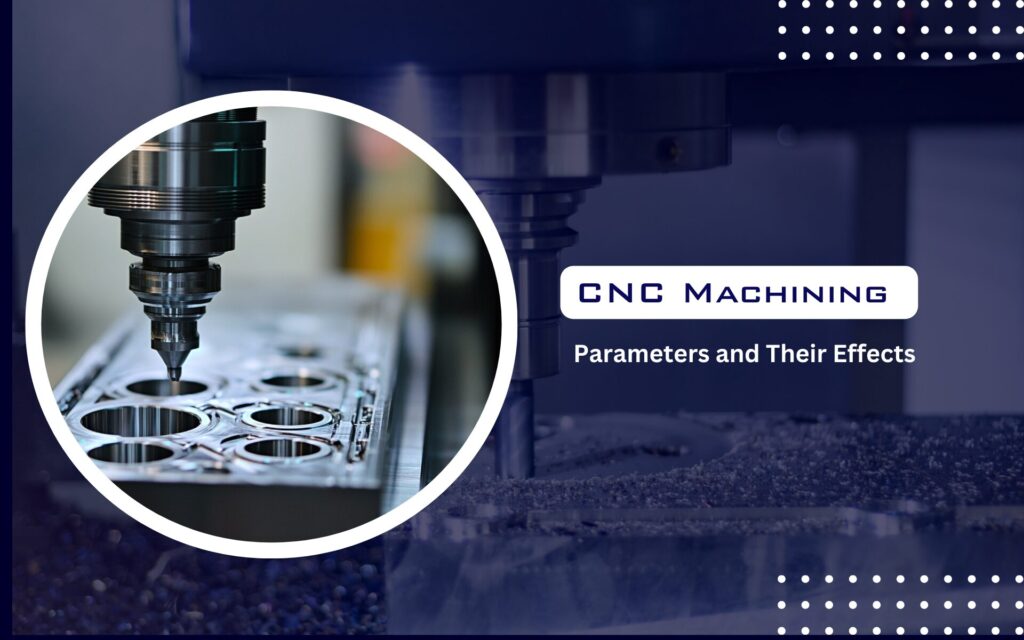
Understanding the impact of each parameter is crucial for optimizing the CNC machining process. Here’s a breakdown of the main parameters and their effects on machining performance:
- Cutting Speed: This is the speed at which the cutting tool engages with the material. It is crucial for efficient material removal and affects the quality of the cut. Higher cutting speeds generally lead to faster production but require careful balancing to avoid excessive heat and tool wear.
- Feed Rate: The feed rate determines how quickly the cutting tool advances into the workpiece. A well-optimized feed rate ensures smooth cutting and minimizes tool wear. Too high a feed rate can cause excessive force and vibrations, while too low a feed rate may lead to inefficient machining and increased production time.
- Depth of Cut: This parameter defines how much material is removed in a single pass. It impacts the efficiency of the machining process and the load on the cutting tool. Properly setting the depth of cut helps in achieving the desired material removal rate and maintaining the tool’s performance.
- Spindle Speed: The rotational speed of the spindle affects both cutting efficiency and tool life. Higher spindle speeds are typically used for softer materials, while lower speeds are suited for harder materials. Correct spindle speed settings help in achieving a smooth surface finish and extending tool life.
- Plunge Rate: This is the rate at which the cutting tool moves vertically into the material. An appropriate plunge rate ensures that the tool cuts efficiently without causing excessive wear or damage. It is especially important for operations like drilling and vertical cutting.
- Tool Path: The tool path is the trajectory that the cutting tool follows to remove material from the workpiece. Efficient tool path planning helps in reducing cycle times and improving surface quality. Tools paths should be optimized to avoid unnecessary movements and minimize machining time.
Best Practices for Optimizing CNC Machining Parameters
To get the most out of your CNC machining process, applying best practices for parameter optimization is essential. Here are some strategies to ensure optimal performance:
- Material Properties: Adjust parameters based on the material’s hardness and properties. Softer materials can often handle higher speeds and feed rates, while harder materials require more conservative settings.
- Tool Condition: Regularly check and maintain cutting tools. Ensure they are sharp and in good condition to achieve optimal performance and extend their lifespan.
- Machine Capabilities: Consider the CNC machine’s power and stability. Machines with higher power can handle more aggressive cutting conditions, while less powerful machines may require more careful parameter adjustments.
- Surface Finish Requirements: Tailor parameters to achieve the desired surface finish. Adjust feed rates and cutting speeds to balance between efficiency and finish quality.
- Monitoring and Adjustments: Continuously monitor machining operations and make adjustments as needed. Regularly review performance and tweak parameters to address any issues and improve overall efficiency.
Conclusion
Understanding and optimizing CNC machining parameters is essential for achieving high-quality results and efficient production. By carefully selecting and adjusting parameters such as cutting speed, feed rate, and spindle speed, manufacturers can enhance precision, prolong tool life, and reduce production costs. Implementing best practices and staying attentive to signs of parameter-related issues will lead to improved machining performance and better overall outcomes.
Have questions or need more information? Feel free to reach out to us through our contact form, and we’ll get back to you as soon as possible.