Introduction
Swiss screw machining, also known as Swiss-type machining, is a high-precision manufacturing process used to produce complex, small parts with tight tolerances. Originating from the Swiss watchmaking industry, this technique has become a staple in many sectors, including medical, aerospace, and electronics, where precision is paramount. In this comprehensive overview, we’ll explore what Swiss screw machining is, its key advantages, common applications, and how it compares to other machining methods.
Advantages
Swiss screw machining offers several benefits that make it a preferred choice for precision manufacturing:
1. High Precision and Tight Tolerances
One of the standout advantages of Swiss screw machining is its ability to achieve extremely tight tolerances.
- Consistent Accuracy: With tolerances as tight as ±0.0001 inches, Swiss screw machines are ideal for producing parts that require high levels of accuracy, such as medical implants and aerospace components.
- Reduced Variability: The design of Swiss screw machines allows for consistent part quality throughout the production run, reducing variability and ensuring uniformity.
2. Capability for Complex Geometries
Swiss screw machines can produce intricate parts with complex shapes and fine details, thanks to their unique design.
- Multiple Axes: Swiss screw machines often feature multiple axes, allowing for complex machining operations like drilling, turning, and milling to be performed simultaneously.
- Live Tooling: These machines can incorporate live tooling, which allows for milling, drilling, and other operations on the same part without removing it from the machine, ensuring accuracy and efficiency.
3. Efficient Production of Small Parts
Swiss screw machining is particularly effective for the production of small, detailed components.
- Rapid Production: With the capability to run at high speeds, Swiss screw machines can quickly produce small parts in large quantities, making them ideal for high-volume production.
- Reduced Cycle Time: The machines’ ability to perform multiple operations simultaneously reduces overall cycle time, enhancing production efficiency.
4. Minimal Material Waste
Swiss screw machining is designed to minimize material waste, making it both cost-effective and environmentally friendly.
- Bar Stock Feeding: The bar stock is fed through a guide bushing, supporting the material close to the cutting tool, which reduces vibration and material loss.
- Precision Cuts: By enabling precise, controlled cuts, Swiss screw machining reduces the amount of material removed, leading to less waste and lower material costs.
5. Reduced Tool Wear
The design of Swiss screw machines reduces the stress on cutting tools, which can lead to longer tool life.
- Stable Workpiece Support: The guide bushing provides continuous support to the workpiece, minimizing deflection and vibration. This helps reduce tool wear and extends tool life.
- Cost Savings: Reduced tool wear translates to lower tooling costs and less downtime for tool changes, making the process more cost-efficient.
Applications of Swiss Screw Machining
Swiss screw machining is used across various industries due to its precision and versatility:
1. Medical Devices and Implants
Swiss screw machining is widely used in the medical field for producing small, high-precision components.
- Surgical Instruments: Swiss screw machines manufacture small surgical instruments like forceps, clamps, and scalpels, ensuring precise cuts and shapes.
- Orthopedic Implants: Precision-machined components such as screws, pins, and plates used in orthopedic surgeries are often made using Swiss screw machining, which guarantees the accuracy required for medical applications.
2. Aerospace Components
The aerospace industry demands components with tight tolerances and high reliability, making Swiss screw machining a preferred manufacturing method.
- Avionics Components: Swiss screw machines produce small avionics components, such as connectors and fasteners, which require high precision to ensure safety and performance in aircraft systems.
- Fuel Injection Parts: Fuel injection components benefit from the accuracy of Swiss screw machining, as they need to fit perfectly to maintain the integrity of the aircraft’s fuel system.
3. Electronics and Telecommunications
Swiss screw machining plays a critical role in the production of small electronic and telecommunications components.
- Connectors and Pins: Precision is crucial for connectors and pins used in electronic devices, and Swiss screw machines can produce these components with high consistency.
- Fiber Optic Connectors: The intricate nature of fiber optic connectors makes them ideal for Swiss screw machining, which can achieve the small diameters and complex shapes required.
4. Automotive Industry
Swiss screw machining is used to manufacture various small, high-precision automotive parts.
- Engine Components: Components like fuel injectors, valve parts, and sensor housings are produced using Swiss screw machining due to the need for tight tolerances and reliable performance.
- Brake System Parts: Parts used in anti-lock braking systems (ABS) and other safety-critical systems benefit from the precision of Swiss machining, ensuring optimal performance and safety.
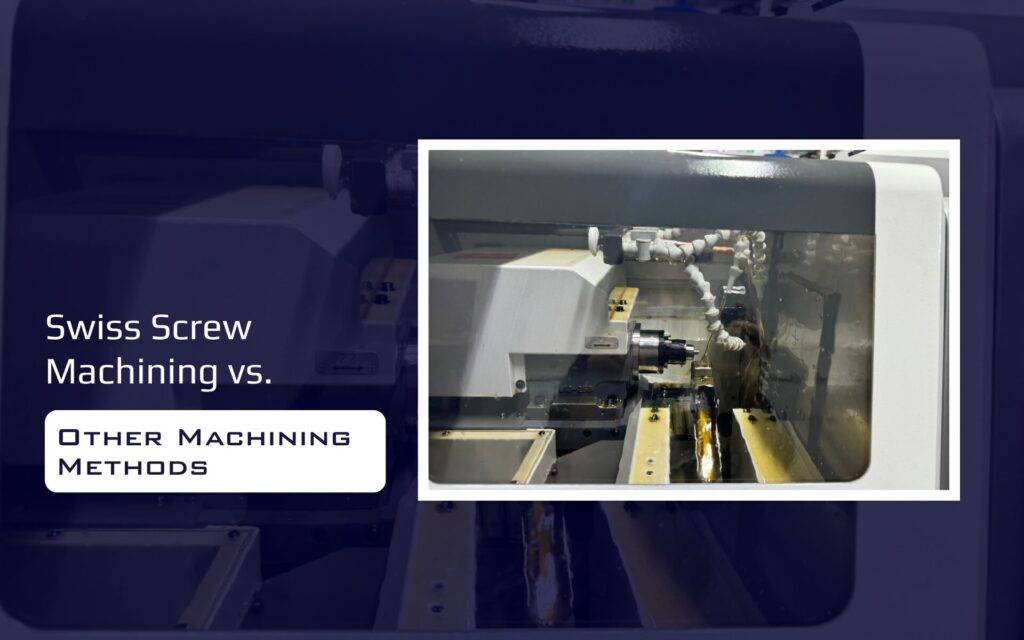
Comparative Analysis: Swiss Screw Machining vs. Other Machining Methods
Swiss screw machining has distinct advantages over other machining techniques. Here’s a comparative analysis:
Feature | Swiss Screw Machining | Traditional CNC Machining | Multi-Spindle Machining |
Precision | High, ideal for tight tolerances | High, but limited by setup changes | Moderate, focused on high-volume |
Part Complexity | Excellent for complex geometries | Good, but with limitations | Limited, mainly for simpler parts |
Material Waste | Minimal, with efficient cuts | Moderate, depending on toolpath | Higher, due to bulk material removal |
Production Speed | Fast for small parts | Moderate, slower for complex parts | Fast for simpler parts |
Tool Wear | Low, due to stable support | Moderate, varies by material | High, due to faster operations |
As the table suggests, Swiss screw machining is optimal for producing small, complex parts with high precision, minimal waste, and low tool wear. While traditional CNC machining and multi-spindle machining have their own benefits, Swiss screw machining stands out for high-precision, small-diameter components that require tight tolerances.
Conclusion
Swiss screw machining is a versatile, high-precision manufacturing method ideal for producing small, complex components across various industries. Its advantages, including tight tolerances, efficient production, minimal material waste, and low tool wear, make it a preferred choice for critical applications in medical, aerospace, electronics, and automotive sectors. As industries continue to demand higher precision and more complex geometries, Swiss screw machining will remain at the forefront of precision manufacturing.
Looking for precision in your manufacturing process? Swiss screw machining offers the solution you need for quality parts and reliable results. Contact us today to learn more!