5 Axis Machining
ProtoTech Machining leads the industry in precision and innovation with our 5-axis machining services, transforming complex designs into tangible masterpieces with unparalleled accuracy and efficiency.
- Save 30% on average
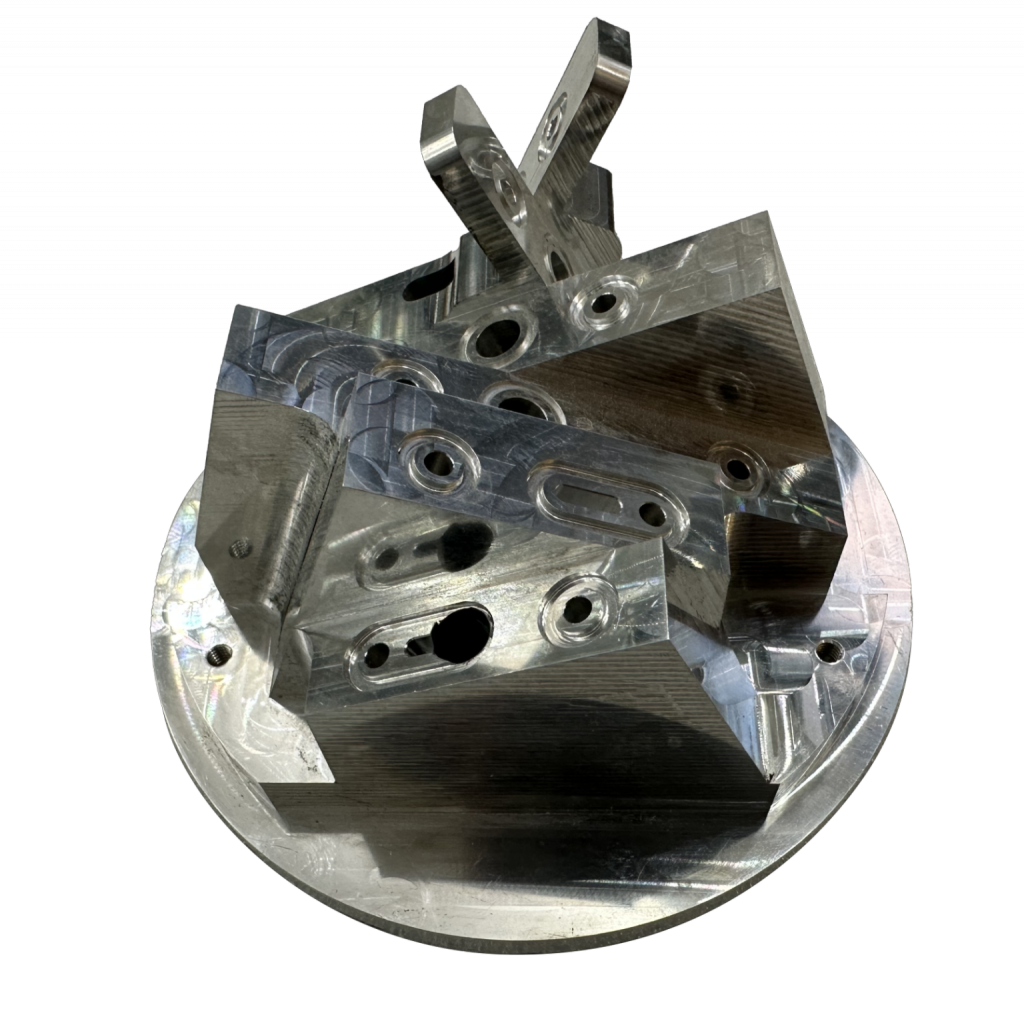
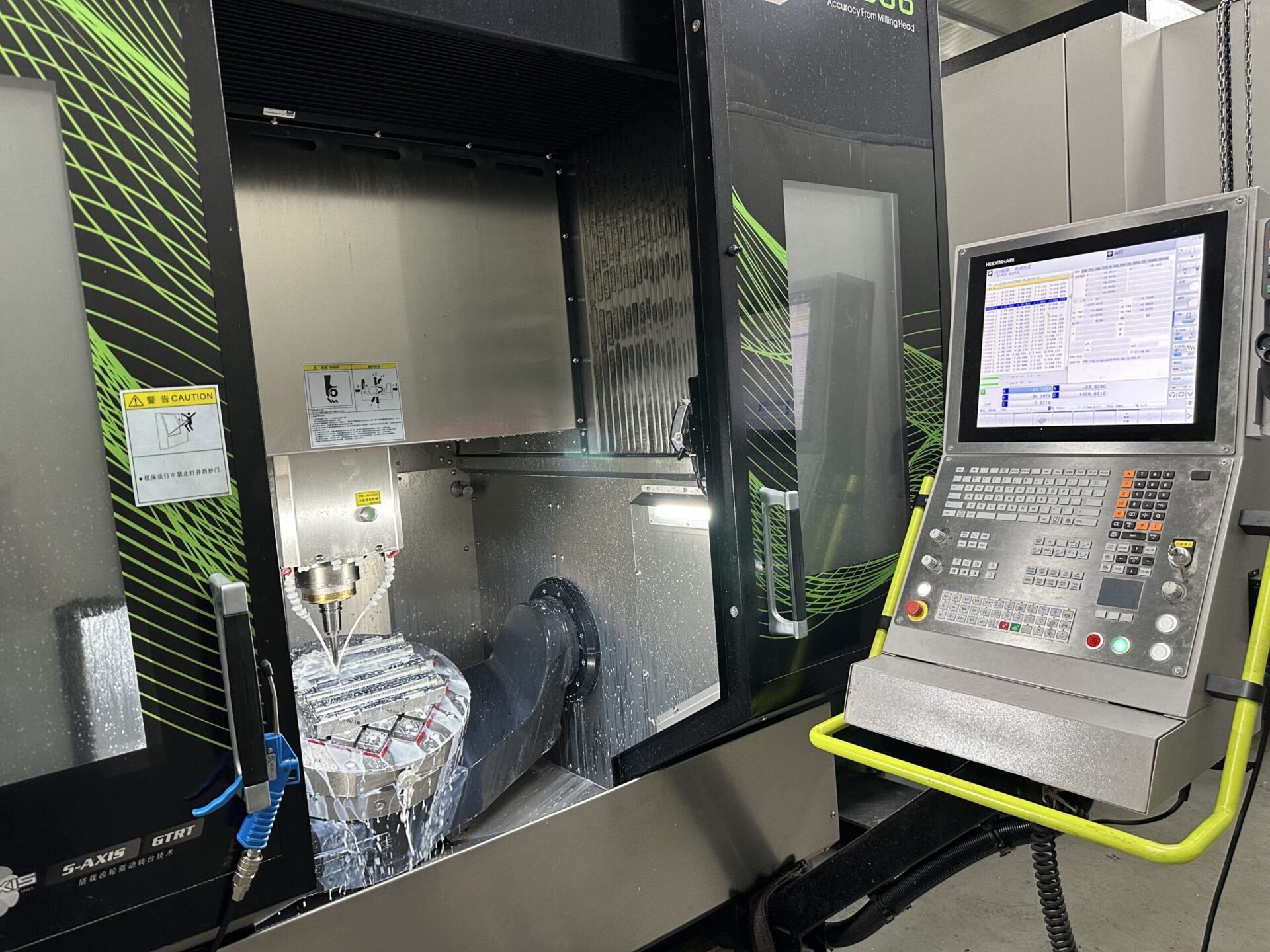
Revolutionizing Precision Manufacturing with 5-Axis CNC Machining
Beyond precision, 5-axis technology offers substantial cost savings. By combining various machining operations into a single setup, it boosts production throughput, reduces cycle time, eliminates costly fixtures, and minimizes overall waste. This efficient and economical approach ensures faster lead times, quicker production turnaround, and exceptional quality compared to standalone horizontal or vertical machining.
Whether aiming for cost efficiency, machining complex parts, achieving extreme tolerances, or a combination, Trace-A-Matic stands as your premier 5-axis machine shop for world-class precision.
Machining Capabilities Summary
Part Types:
Part Size (work envelope):
Metal Types:
Material Types:
Castings, forgings, fabricated weldments, billets, and bar stock
5-Axis Processes:
Industries Served:
Machine Brands:
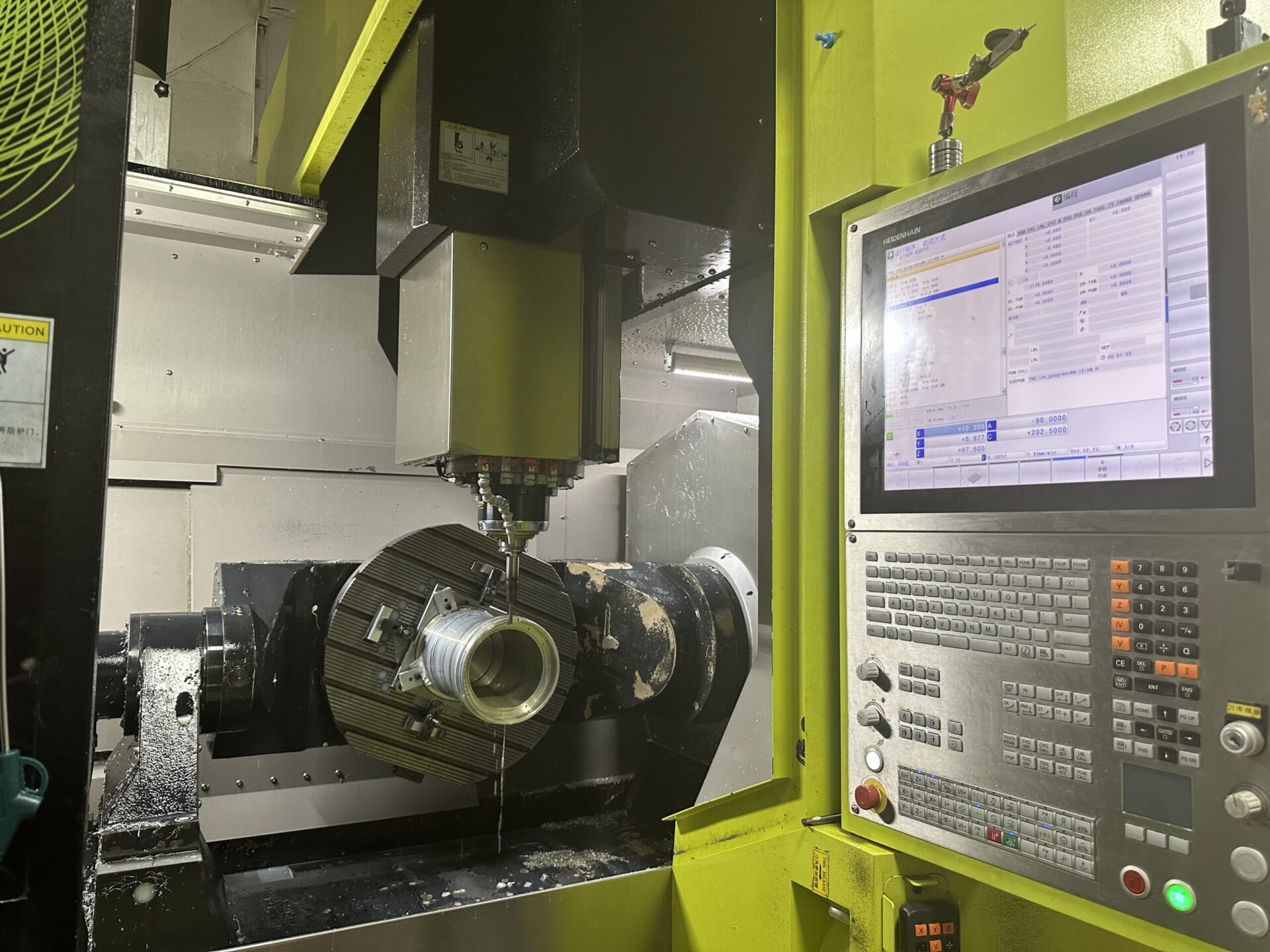
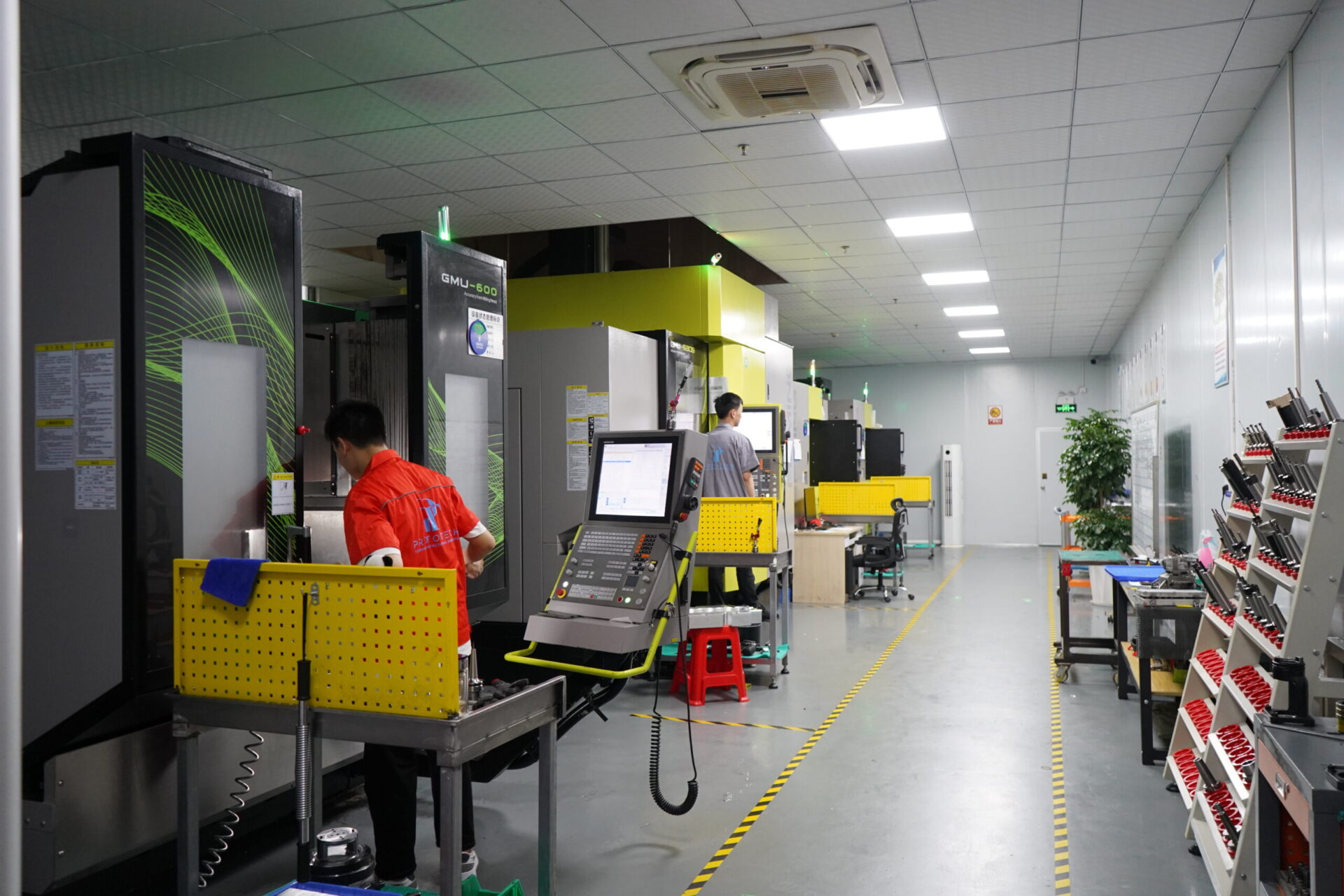
Exploring 5-Axis CNC Machining
A 5-axis machining center features a variable-speed tool spindle head with multidirectional rotary axes orientation. Raw material securely clamps into an indexing chuck or onto a table. The spindle head assembly moves in tandem with the chuck or index table along the travel columns, precisely manipulating the workpiece and cutting tool to achieve the required tool path for material removal. 5-axis machines enable single setups, infinite geometry cutting, efficient chip management, extended tool life, repeatable manufacturing, and high-speed simultaneous 5-axis precision machining. Similar to standard milling and turning machines, this process follows subtractive manufacturing principles.
Anatomy of a 5-Axis Machine
- Rotary Spindle Head:
Variable-speed spindle housing a rotating cutting tool.
Travels on the Y-axis (front to back) and spins on the B-axis. - Cutting Tool:
Machine tools responsible for subtractive manufacturing, cutting material from the workpiece to shape the part.
- Traveling Columns:
The Z-axis (left to right) and X-axis (top to bottom) columns facilitate the movement of the rotary spindle head and tooling.
- Main Spindle:
Primary chuck holding the workpiece, capable of rotating on the C-axis at speeds up to 2,500 RPMs and moving on the Z-axis.
- Sub-Spindle:
Secondary chuck holding the workpiece, able to revolve on the C-axis at speeds up to 2,500 RPMs and move on the Z-axis.
- CNC Control Panel:
The interface used by machinists to program and control the operations of a computer numerical control (CNC) machine.
Advantages of 5-Axis Machining
5-Axis Machining Benefits
- Highly Engineered and Complex Part Machining: Precision machining of intricate and complex parts.
- Create Complex Part Geometry in One Operation: Achieve intricate part geometry efficiently in a single operation.
- Increased Part Accuracy: Improved accuracy in part production.
- Reduced Part Handling, Setups, and Fewer Machines Used: Streamlined processes with fewer setups, reducing part handling and machine requirements.
- Producing Parts Complete on Demand: Efficient production of complete parts as needed.
- Reduction of Costly Workpiece Fixtures and Tooling Redundancy: Minimized reliance on expensive workpiece fixtures and redundant tooling.
- Less Ancillary Equipment Needed – Gages and Tools: Reduced dependency on additional equipment like gauges and tools.
- Conducive to Unattended Operations – Single Point Load / Unload: Facilitates unattended operations with a single point for loading and unloading.
- Improved Traceability and Documentation – Done-in-One: Enhanced traceability and documentation with all-in-one machining.
- Go All the Way – Hobbing, Gear Cutting, and Skiving: Capability to perform diverse operations including hobbing, gear cutting, and skiving.
- Design for Manufacture: Collaborate for efficient component design, eliminating geometric inconsistencies caused by multiple operations.
Design for Manufacture
- Collaborate to design components more mechanically or ergonomically efficient.
- Eliminate built-in geometrical inconsistencies or errors caused by multiple operations, providing faster, more straightforward programs and more accurate parts.
- Accelerate product development and time to market by testing and altering designs quickly and easily.
- Enable engineers to enhance component design, such as integral gear or spline improvements, without manufacturing restrictions imposed by machine tool kinematics and capability.
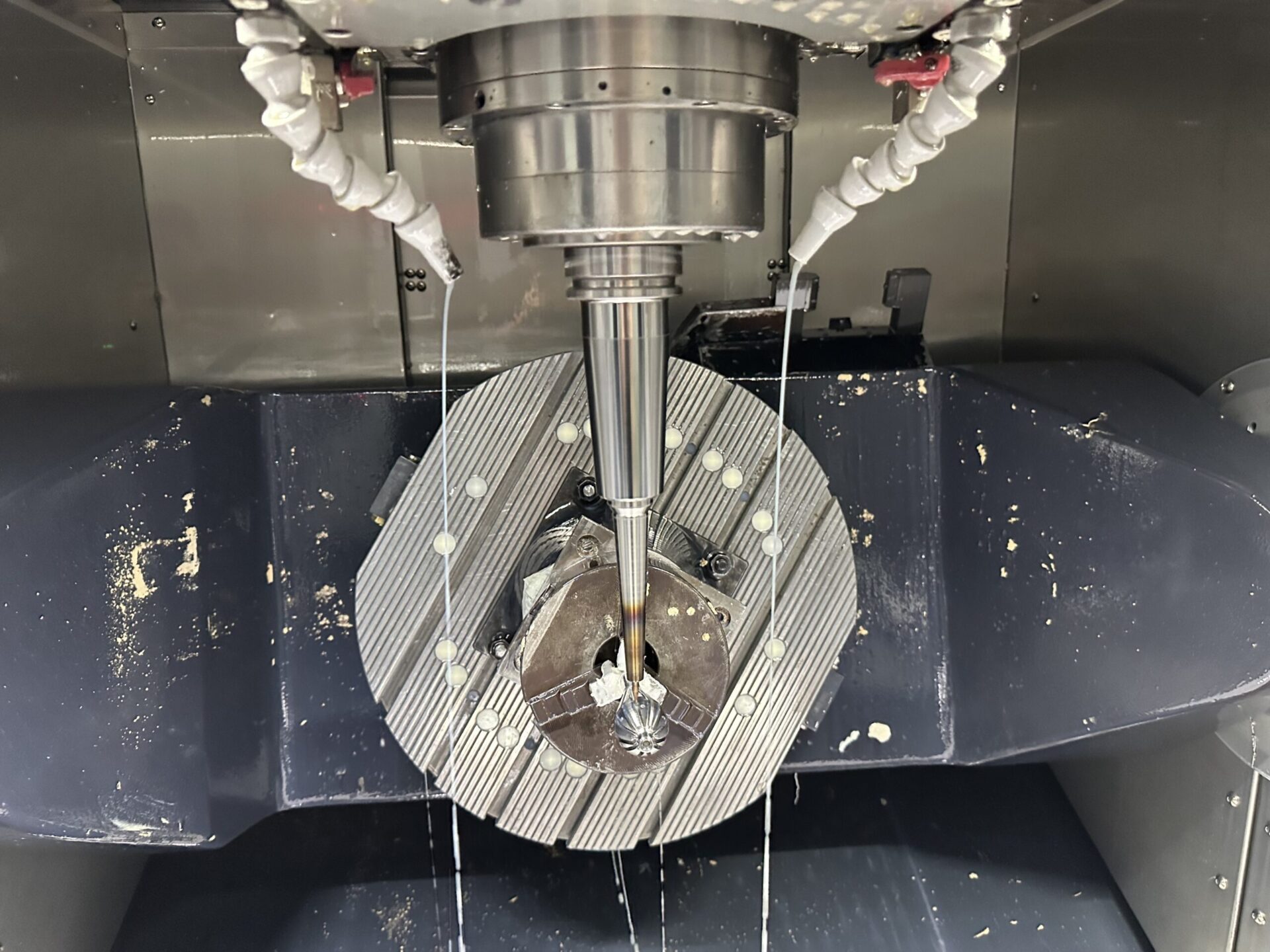
Automation in 5-Axis Machining: Mazak HCR-5000
Complex Part Machining
Optimized for Aluminum Components
Work Envelope: Up to 28.74” x 28.74”
Automation: 18 Pallet System
Queued Operations for 18 Jobs
Minimizes Non-Cut Time
Improves Overall Process Efficiency
High-Efficiency Cooling System
Reduces Thermal Growth
High Accuracy and Efficiency
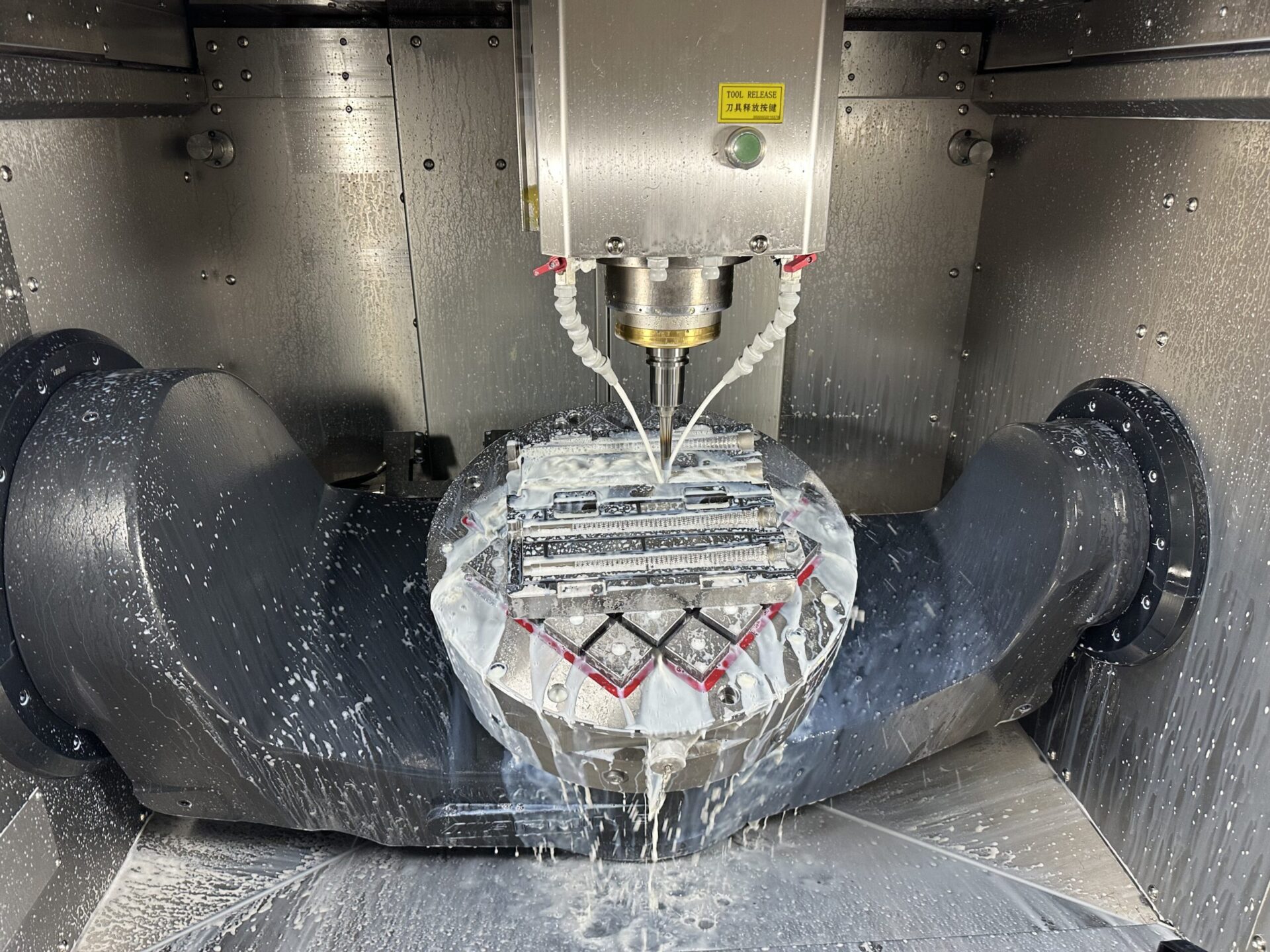
6-Sided Complete Machining: DMG Mori CTX TC (4 Units)
Complex Part Machining
High Precision and Throughput
Work Envelope: Up to 120.1” x 27.5” (19.7” Chuck)
Machining Versatility
Fully Prismatic Parts From Raw Material
High-Powered Turning Center
Elimination of Multiple Setups
Reduced Part Handling
High Part Accuracy
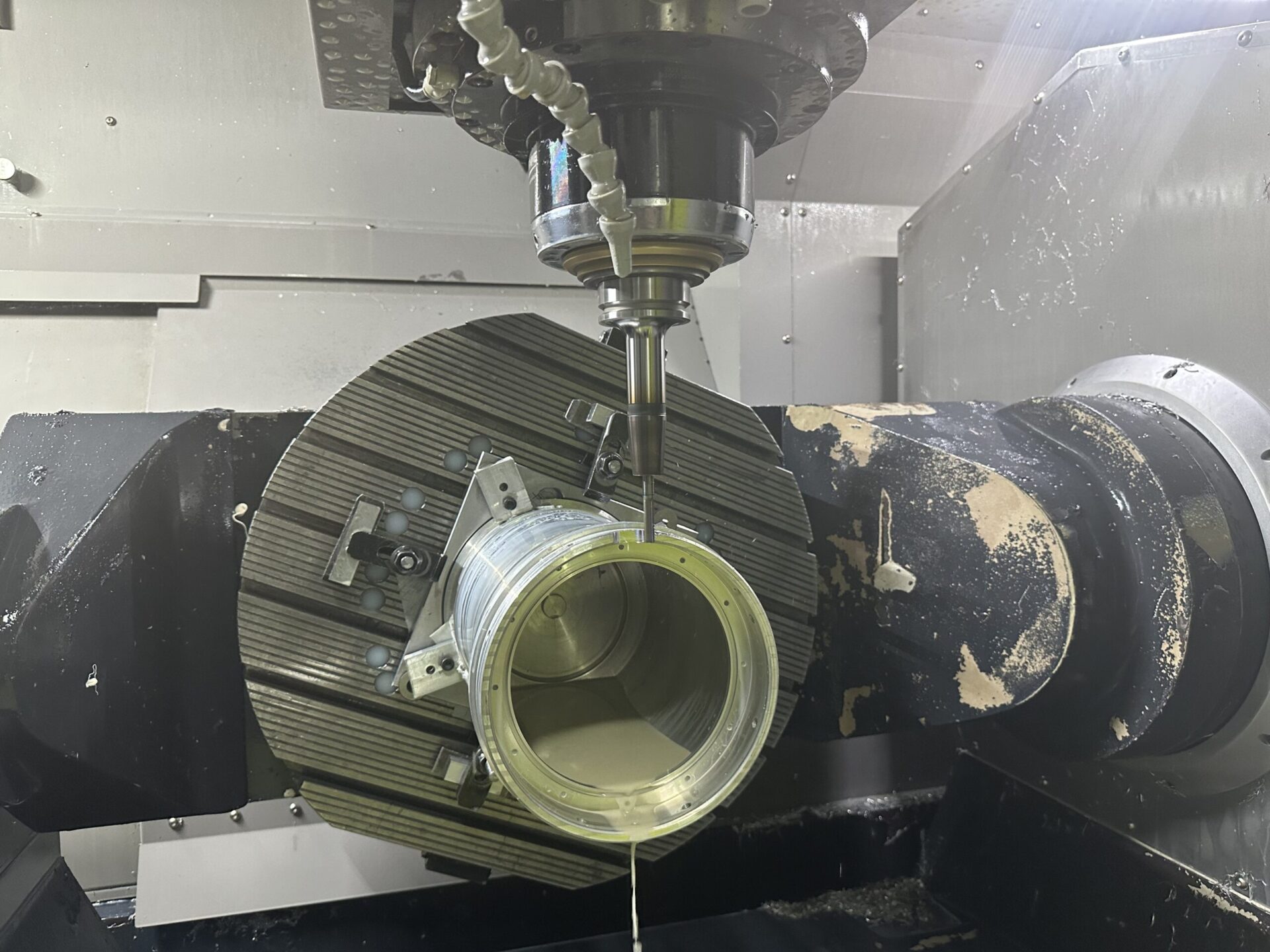
5-Axis Multi-Task Machining: Mazak INTEGREX i-400 (3 Units)
Complex Part Machining
High Precision and Throughput
Work Envelope: Up to 60” x 25.9” (12” Chuck)
High Part Accuracy
Elimination of Multiple Setups
Reduced Part Handling
Improved Efficiency
Reduced Lead-Time
Streamlined Tooling
Minimized Non-Cut Time
Elimination of Fixtures
Gallery Of 5 AXIS MACHINING
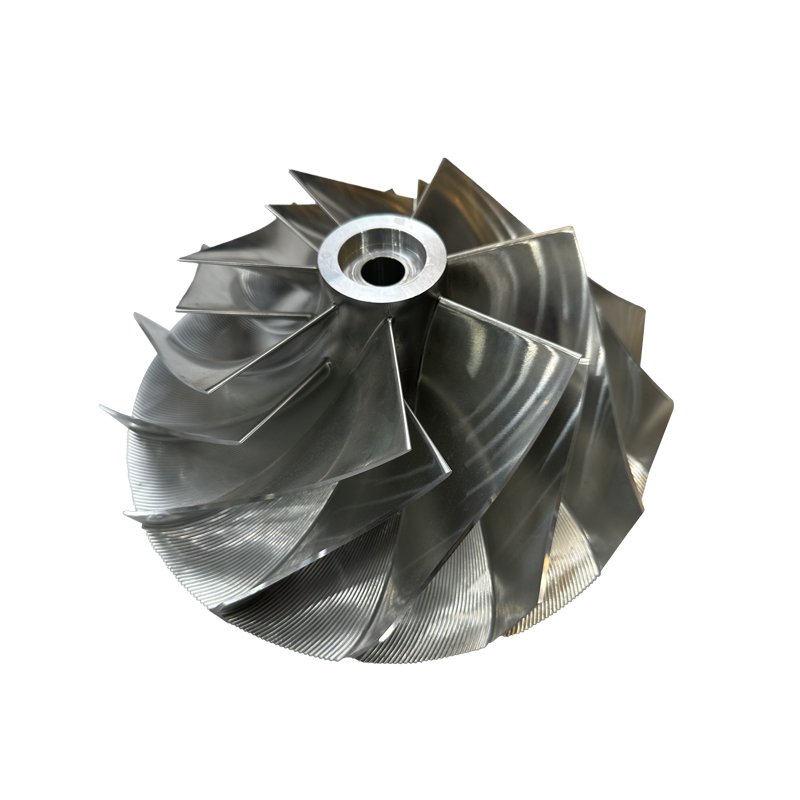
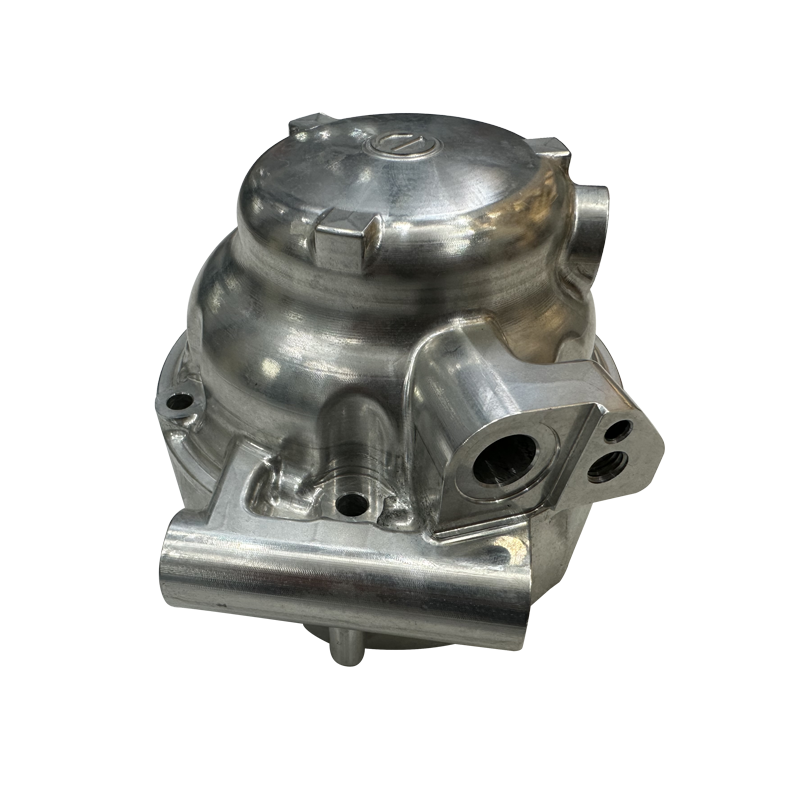
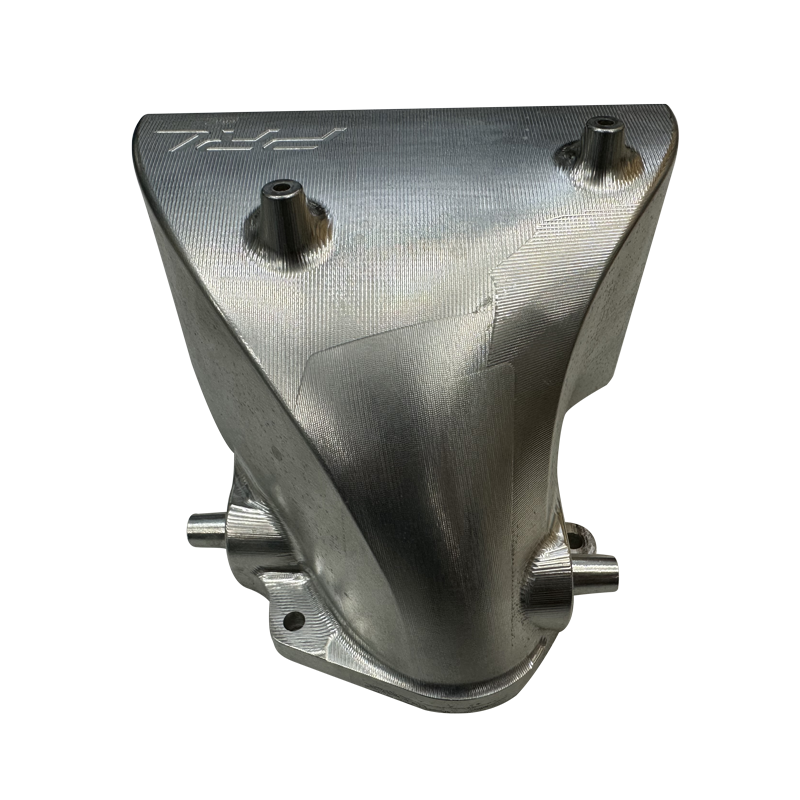

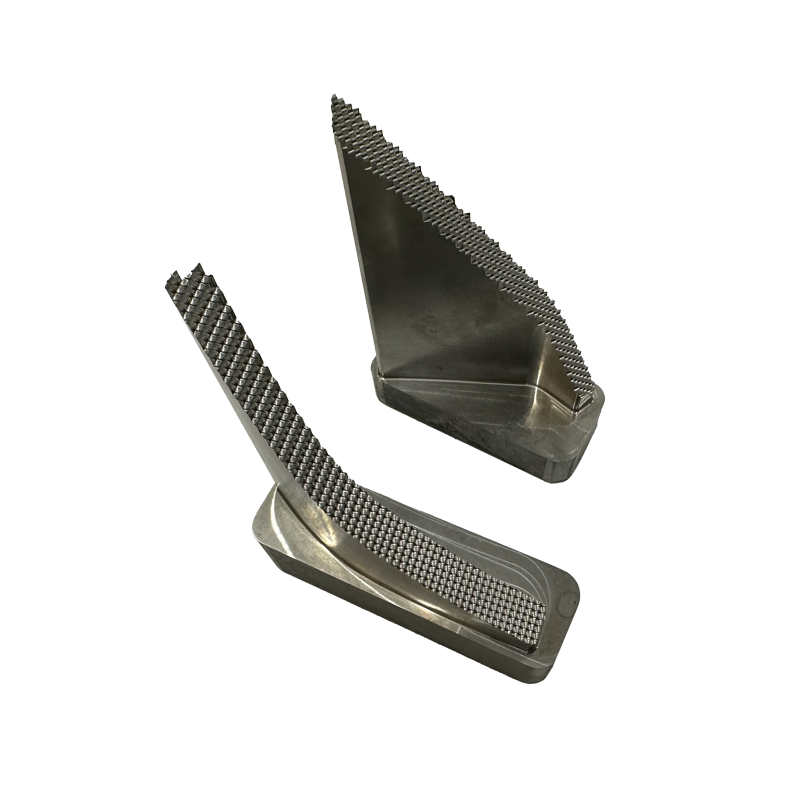
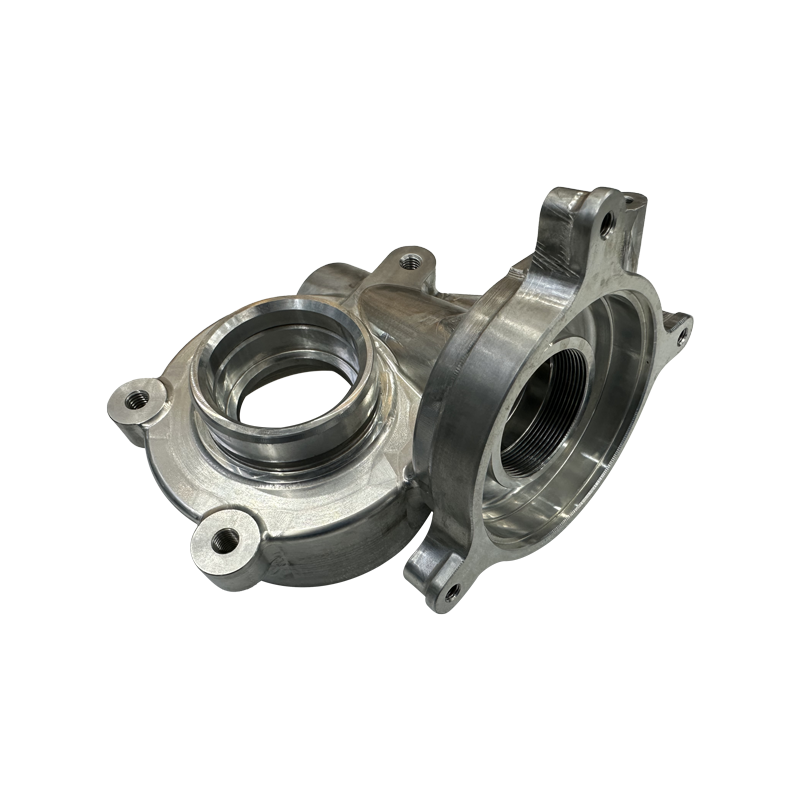
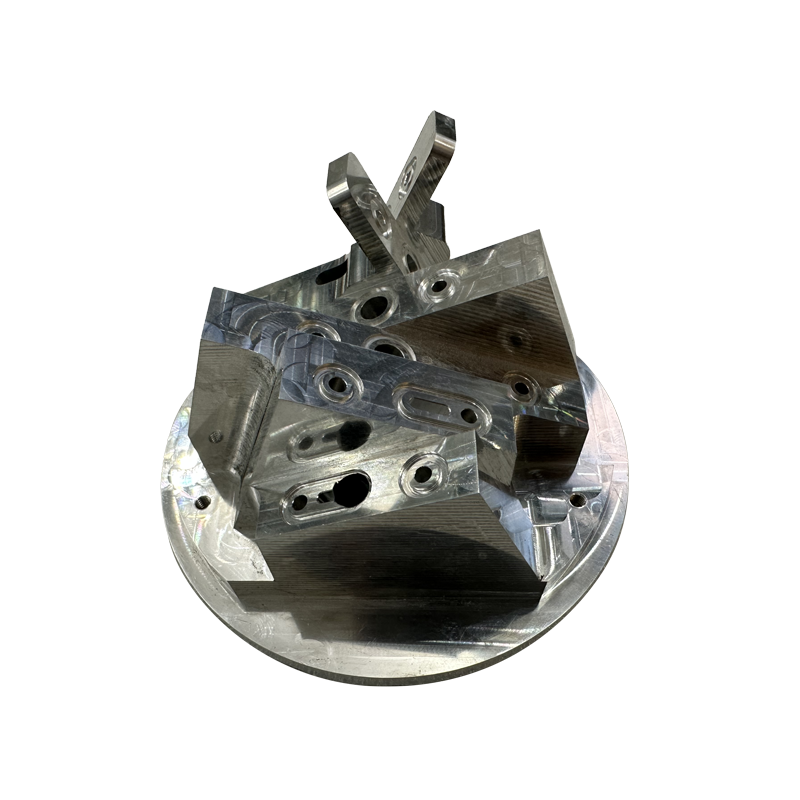