When it comes to engineering and manufacturing, one of the most crucial factors in choosing the right material is its tensile strength. Material with Greatest Tensile Strength refers to a material’s ability to resist breaking under tension, or in simpler terms, how much stretching a material can withstand before failing. This property is essential in determining whether a material can handle specific mechanical stresses, ensuring the safety and durability of products, especially in industries such as aerospace, automotive, construction, and military. In this comprehensive guide, we will explore the material with the greatest tensile strength, providing a detailed look at various metals, alloys, and fibers that dominate the tensile strength chart.
1. Understanding Material with Greatest Tensile Strength
Before diving into the materials with the greatest tensile strength, it’s important to fully understand what tensile strength is and how it is measured.
Definition of Tensile Strength Tensile strength is the maximum amount of tensile (pulling) stress a material can withstand before breaking or fracturing. It is typically measured in megapascals (MPa) or pounds per square inch (psi). The higher the tensile strength, the stronger the material will be under stretching forces.
There are three key types of tensile strength:
- Yield Strength: This refers to the point at which a material begins to deform permanently under stress. It’s the point where the material starts to “yield” or bend.
- Ultimate Tensile Strength (UTS): This is the maximum amount of stress a material can withstand before it breaks. It is the peak on a stress-strain curve.
- Breaking Strength: Also referred to as fracture strength, it’s the point where a material ultimately fails, or fractures under the application of tensile stress.
Factors Affecting Tensile Strength
- Material Composition: The elements that make up the material significantly influence its tensile strength. For example, metals like tungsten and titanium have naturally higher tensile strength due to their atomic structure.
- Temperature: Higher temperatures can reduce a material’s tensile strength. Materials like metals lose their tensile strength at elevated temperatures, which is a critical factor in industries like aerospace.
- Processing: The way materials are processed also plays a role. For instance, heat treatments like quenching or alloying can increase tensile strength.
- Thickness and Size: The shape and size of the material can affect its tensile strength, as thicker materials can generally withstand more stress.
2. Types of Tensile Strength
Now that we have a clear understanding of tensile strength, it’s essential to differentiate between the various types of strength that materials exhibit.
Yield Strength
Yield strength is the point at which a material begins to deform plastically. The yield strength is important when designing parts that must not deform under load. For example, materials used in construction must have high yield strength to avoid bending under weight.
Ultimate Tensile Strength (UTS)
This is the maximum amount of stress a material can bear before it starts to break. UTS is crucial when working with materials that will be subjected to extreme tension. It’s especially relevant for metals used in high-stress applications such as aerospace and military components.
Breaking Strength
Breaking strength refers to the amount of force required to completely fracture a material. While it’s an important factor for understanding how a material fails, it’s typically less important than yield strength and UTS in practical applications.
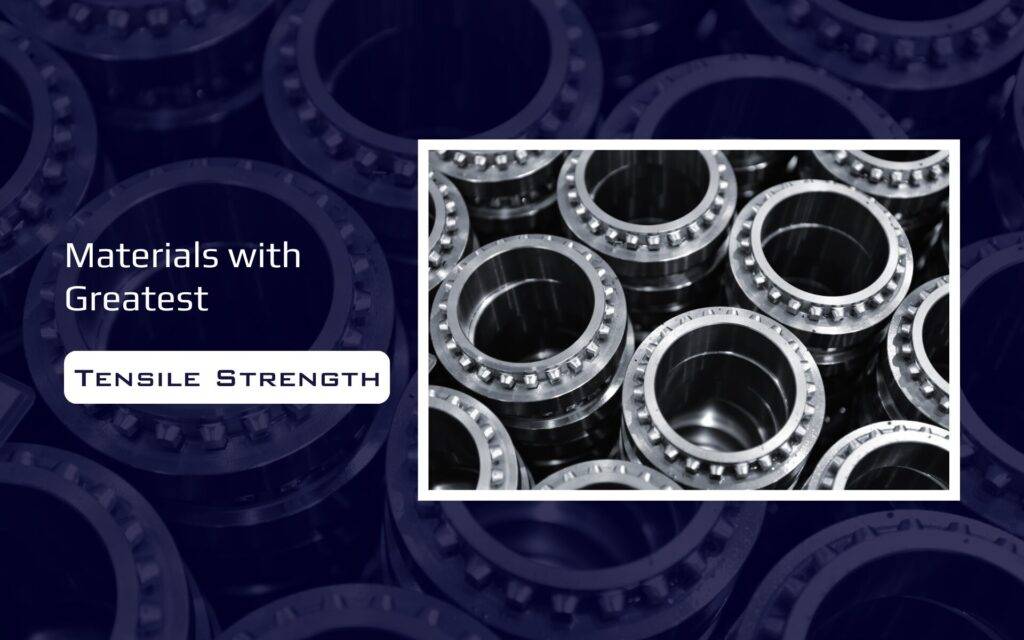
3. Materials with the Greatest Tensile Strength
Let’s take a look at some of the materials with the greatest tensile strength, and why they are ideal for various applications.
Graphene
- Tensile Strength: 130 GPa
- Properties: Graphene is a one-atom-thick sheet of carbon atoms arranged in a hexagonal lattice. It is known for being incredibly strong and light.
- Applications: Electronics, aerospace, medical devices, and more. Graphene’s remarkable strength-to-weight ratio makes it a perfect candidate for use in a variety of high-performance applications.
- Why It’s Strong: The strength of graphene comes from its atomic structure. The carbon-carbon bonds in graphene are incredibly strong, allowing it to withstand extreme tension without breaking.
Carbon Nanotubes (CNTs)
- Tensile Strength: 60 GPa
- Properties: Carbon nanotubes are cylindrical structures made from carbon atoms. They possess a remarkable strength-to-weight ratio and are among the strongest materials known.
- Applications: Reinforcement in composites, aerospace, electronics, and more. CNTs are often used in materials that need to be both strong and lightweight.
- Why It’s Strong: Like graphene, carbon nanotubes benefit from strong carbon-carbon bonds, which give them exceptional tensile strength despite their minimal weight.
Tungsten
- Tensile Strength: 1,725 MPa
- Properties: Tungsten is an incredibly dense metal with a very high melting point. It is often alloyed to enhance its properties.
- Applications: Aerospace, military, mining, and manufacturing of heavy-duty machinery. Tungsten is often used for its strength and high-temperature resistance.
- Why It’s Strong: Tungsten’s tensile strength is a result of its atomic structure and the metallic bonding between tungsten atoms. Its density and atomic arrangement make it incredibly resistant to deformation under tension.
Titanium
- Tensile Strength: 1,400 MPa
- Properties: Titanium is lightweight, highly resistant to corrosion, and offers a favorable strength-to-weight ratio.
- Applications: Aerospace, military, medical implants, automotive. Titanium is used in high-performance applications where strength and weight need to be balanced.
- Why It’s Strong: Titanium’s strength comes from its unique atomic structure, which gives it a high tensile strength-to-density ratio, making it an excellent material for weight-sensitive applications.
High Carbon Steel
- Tensile Strength: 2,500 MPa
- Properties: High carbon steel is known for its hardness and high strength. The carbon content can be adjusted to enhance its properties.
- Applications: Construction, automotive, and manufacturing. High carbon steel is often used in applications that require both strength and toughness.
- Why It’s Strong: The higher the carbon content, the stronger the steel becomes. The presence of carbon makes the metal more resistant to deformation, contributing to its high tensile strength.
Stainless Steel
- Tensile Strength: 1,600 MPa
- Properties: Stainless steel is an alloy of steel that contains chromium, which gives it excellent corrosion resistance.
- Applications: Medical instruments, aerospace components, food industry equipment, and more.
- Why It’s Strong: The alloying of chromium with steel makes stainless steel not only strong but also resistant to rust, corrosion, and staining, which makes it ideal for demanding applications.
Titanium Alloys
- Tensile Strength: 1,100 MPa to 1,400 MPa
- Properties: Titanium alloys are lighter than many other metals, yet still very strong and corrosion-resistant.
- Applications: Aerospace, military, automotive, and medical fields.
- Why It’s Strong: The strength of titanium alloys comes from the blending of titanium with elements like aluminum and vanadium, which enhances its properties.
4. Comparison of Material Tensile Strength
To better understand how these materials compare, let’s look at them side by side.
- Graphene vs. Carbon Nanotubes: While graphene has a higher tensile strength, carbon nanotubes are also extremely strong and are more easily incorporated into composite materials.
- Tungsten vs. Titanium: Tungsten has a higher tensile strength, but titanium is much lighter, making it the preferred material for aerospace and automotive industries where weight is a significant consideration.
- High Carbon Steel vs. Stainless Steel: High carbon steel has a higher tensile strength, but stainless steel offers better corrosion resistance, making it more versatile for a wider range of applications.
5. How Tensile Strength Affects Material Selection
Tensile strength is one of the most important properties when selecting materials for engineering applications. The higher the tensile strength, the more stress a material can endure before failure.
Engineering and Construction
For structural components that must bear heavy loads, materials with high tensile strength are crucial. For example, steel and titanium alloys are often used in large bridges, buildings, and infrastructure projects due to their superior strength.
Aerospace and Military
In aerospace, materials must be lightweight yet capable of withstanding extreme forces. Titanium, carbon fiber, and composites made with carbon nanotubes are frequently used in these applications.
Automotive and Manufacturing
In automotive manufacturing, high tensile strength materials like high carbon steel and stainless steel are used for body panels, engine components, and other critical parts that require both strength and formability.
Medical Applications
In medical applications, materials like titanium are used for implants due to their biocompatibility, strength, and resistance to corrosion.
6. Testing and Measuring Tensile Strength
Tensile strength is typically measured using a tensile test, where a sample is pulled until it breaks. The stress-strain curve generated from this test can provide valuable information about a material’s behavior under tension, including its yield point, ultimate tensile strength, and breaking strength.
Key Testing Methods
- Universal Testing Machine (UTM): The UTM is used to apply a controlled force to a material while measuring its response. The force is gradually increased until the material fractures.
- Stress-Strain Curves: These curves are used to plot the material’s response to stress, helping engineers determine important points like yield strength and ultimate tensile strength.
7. The Future of High-Tensile Strength Materials
As technology advances, we can expect new materials with even higher tensile strength to be developed. The future of tensile strength in materials lies in:
- Graphene and Carbon Nanotubes: As research advances, graphene and carbon nanotubes are expected to become more widely used in everyday applications.
- Nanotechnology: Advances in nanotechnology are poised to bring about new materials with outstanding strength-to-weight ratios.
- Sustainability: The development of stronger, more sustainable materials will help create more efficient and environmentally friendly designs.
Conclusion
Understanding the materials with the greatest tensile strength is crucial for making the best material choice for your projects. Whether it’s the aerospace industry, construction, medical applications, or automotive manufacturing, tensile strength is a critical factor in ensuring safety, durability, and performance.
By selecting the right material based on tensile strength, engineers and manufacturers can optimize designs, reduce material waste, and create products that stand the test of time. As we move into the future, advancements in materials science will continue to unlock new possibilities for stronger, more efficient materials.