High-gloss polishing is essential in CNC machining for achieving mirror-like finishes that enhance both the visual appeal and functionality of parts. This technique is crucial in industries like aerospace, automotive, and consumer electronics. This comprehensive guide will cover best practices, tools, and techniques to ensure your CNC-machined components not only look impressive but also perform optimally. Whether you’re refining your skills or aiming to optimize your manufacturing processes, this guide provides all the insights you need.
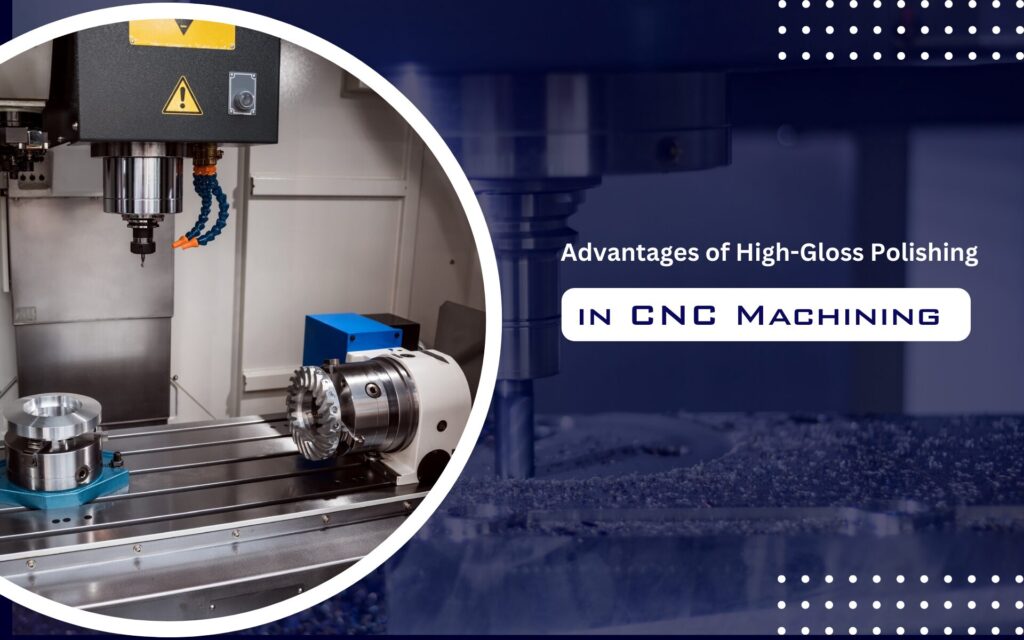
Why High-Gloss Polishing Matters in CNC Machining
High-gloss polishing offers a range of benefits that extend beyond aesthetic enhancement. Here’s how this finishing technique contributes to the performance and longevity of CNC-machined parts:
Improved Light Reflection and Heat Resistance
Polishing enhances light reflection, beneficial for optical devices and automotive components. Additionally, it can improve heat resistance, helping maintain performance and prevent damage in high-temperature applications.
Superior Aesthetic Appeal
A mirror-like finish significantly enhances the appearance of components, making them look sophisticated and premium. In consumer-facing industries, such as electronics and automotive, a polished surface adds considerable value to products.
Enhanced Durability and Performance
By reducing surface roughness, polishing minimizes stress concentration points that can lead to material fatigue or failure. This results in more durable components that maintain their integrity, which is vital for sectors like medical devices and aerospace.
Easier Cleaning and Maintenance
The smooth, high-gloss surface is easier to clean and maintain, making it ideal for environments requiring high cleanliness standards, such as food processing and medical facilities.
The Role of CNC Machining in Achieving High-Gloss Finishes
Achieving a high-gloss finish in CNC machining involves more than just precision cutting. Here’s how CNC machining integrates with high-gloss polishing to deliver superior results:
Starting with the Basics: Sanding and Smoothing
The path to a high-gloss finish begins with thorough sanding. This initial step removes any marks or roughness from the CNC machining process. Using progressively finer grits, such as 2000-grit sandpaper, ensures that the surface is smooth and prepared for high-gloss polishing.
Transition to High-Gloss Polishing
Once the surface is prepped, high-gloss polishing is applied to achieve the mirror-like finish. This step is crucial for components like transparent light guides and lenses, where a flawless, reflective surface is essential. High-gloss polishing not only enhances the appearance but also ensures the functional integrity of these parts.
Additional Surface Enhancements
Beyond high-gloss polishing, CNC machining services often offer additional finishing options, such as sandblasting and painting. These techniques can further refine surface texture, add aesthetic elements, or provide specific functional benefits, depending on the application.
Applications Where Mirror-Like Finishes Work Best
Mirror-like finishes achieved through high-gloss polishing have practical and aesthetic benefits across various industries. Here’s where these finishes are most effective:
1. Automotive Industry In the automotive sector, high-gloss finishes are valued for both exterior and interior components. Polished body panels, trim, and chrome accents not only enhance the visual appeal but also reduce drag, contributing to improved aerodynamics.
2. Medical Devices For medical devices and tools, high-gloss finishes are essential for easy sterilization and maintenance. The smooth surface resists contaminants, ensuring that devices meet stringent hygiene standards. This finish is particularly important for surgical instruments, implants, and diagnostic equipment.
3. Aerospace Components Aerospace applications require components that are both lightweight and durable. High-gloss polishing provides a smooth surface that reduces friction and enhances wear resistance, making it ideal for turbine blades, engine components, and other critical aerospace parts.
Conclusion
Mastering high-gloss polishing in CNC machining is key to achieving components that not only look exceptional but also perform at their best. By understanding the techniques and applications of high-gloss polishing, manufacturers can elevate their product quality, meet rigorous industry standards, and enhance functionality.
As technology advances and industry demands evolve, the role of high-gloss polishing will continue to grow. Embrace this process to boost your manufacturing capabilities, improve durability, and achieve that perfect mirror-like finish. For expert advice and more insights on high-gloss polishing, contact us to take your CNC machining capabilities to the next level.
For more information, visit: https://prototech-machining.com/services/surface-finishing/