Introduction
In the world of automotive performance, weight reduction and strength are two of the most sought-after characteristics for improving speed, efficiency, and handling. Enter custom carbon fiber car parts: lightweight yet incredibly strong, carbon fiber components have revolutionized car design and performance. This article delves into the benefits of custom carbon fiber parts, explores the manufacturing processes behind them, and highlights real-life applications that showcase their impact.
Benefits of Custom Carbon Fiber Parts
Carbon fiber is a composite material known for its unique combination of strength and low weight. Here’s why custom carbon fiber car parts have become a preferred choice in the automotive industry:
1. Lightweight Construction
The primary advantage of carbon fiber is its lightweight nature, which has a significant impact on vehicle performance.
- Improved Speed: Reducing the weight of a vehicle translates into better acceleration, higher top speeds, and improved overall handling.
- Enhanced Fuel Efficiency: Lighter vehicles require less energy to move, leading to better fuel economy and reduced emissions.
2. Exceptional Strength and Durability
Despite its low weight, carbon fiber boasts impressive strength, often exceeding that of steel and aluminum.
- High Tensile Strength: Custom carbon fiber car parts can withstand high stress and mechanical loads, making them ideal for critical components like chassis reinforcements, driveshafts, and body panels.
- Impact Resistance: Carbon fiber’s high energy absorption capacity provides greater safety in crash scenarios, as it can absorb and distribute impact forces more effectively than traditional materials.
3. Aerodynamic Design
Carbon fiber’s flexibility during the manufacturing process allows for more precise and aerodynamic designs.
- Streamlined Shapes: Carbon fiber parts can be molded into complex, streamlined shapes that reduce drag and improve downforce, enhancing vehicle stability and handling at high speeds.
- Custom Fit: Unlike standard parts, custom carbon fiber components can be tailored to fit specific vehicle models or even individual modifications, ensuring optimal aerodynamic performance.
4. Corrosion Resistance
Carbon fiber is naturally resistant to corrosion, making it a durable option for both exterior and interior car parts.
- Extended Lifespan: Unlike metals that can rust over time, carbon fiber maintains its integrity even when exposed to moisture, chemicals, and other harsh conditions.
- Minimal Maintenance: The corrosion-resistant nature of carbon fiber parts reduces the need for frequent maintenance or replacements, making them a cost-effective choice in the long run.
5. Aesthetic Appeal
Carbon fiber is not just about performance—it also adds a distinct visual appeal to vehicles.
- Sleek, High-Tech Look: The signature weave of carbon fiber offers a sporty, high-tech aesthetic that appeals to automotive enthusiasts.
- Customization Options: Custom carbon fiber parts can be clear-coated, painted, or left in their raw, glossy state to enhance a vehicle’s overall appearance.
Manufacturing Processes for Carbon Fiber Parts
Creating custom carbon fiber car parts is a meticulous process that requires precision and expertise. Here’s an overview of the most common manufacturing methods:
1. Hand Lay-Up
The hand lay-up process is one of the simplest and most cost-effective ways to produce custom carbon fiber parts.
- Process Overview: In this method, carbon fiber sheets are manually placed into molds, which are then coated with resin. The parts are left to cure, forming a solid and lightweight structure.
- Best For: Hand lay-up is ideal for creating large parts like hoods, trunk lids, and body panels, where a high level of detail is not required.
2. Resin Transfer Molding (RTM)
RTM is a more advanced process that offers greater precision and consistency.
- Process Overview: In RTM, carbon fiber fabrics are placed into a mold, and resin is injected under pressure, ensuring an even distribution throughout the part.
- Advantages: This method produces parts with a smooth surface finish and enhanced strength, making it suitable for structural components like roll cages and suspension arms.
3. Autoclave Molding
Autoclave molding is considered the gold standard in carbon fiber manufacturing, often used for high-performance automotive and aerospace components.
- Process Overview: Carbon fiber layers are placed into molds and then subjected to high pressure and heat in an autoclave, which results in a stronger bond between the fibers and the resin.
- Best For: This method is used to create lightweight yet incredibly strong parts, such as race car monocoques, roof panels, and fenders.
4. Prepreg Lamination
Prepreg lamination involves the use of pre-impregnated carbon fiber sheets that already contain the resin.
- Process Overview: The prepreg sheets are laid into molds, then cured in an autoclave or oven to form the final part.
- Advantages: This technique allows for the creation of complex parts with a high degree of precision and minimal resin waste, making it suitable for custom interior components, wings, and other performance-oriented parts.
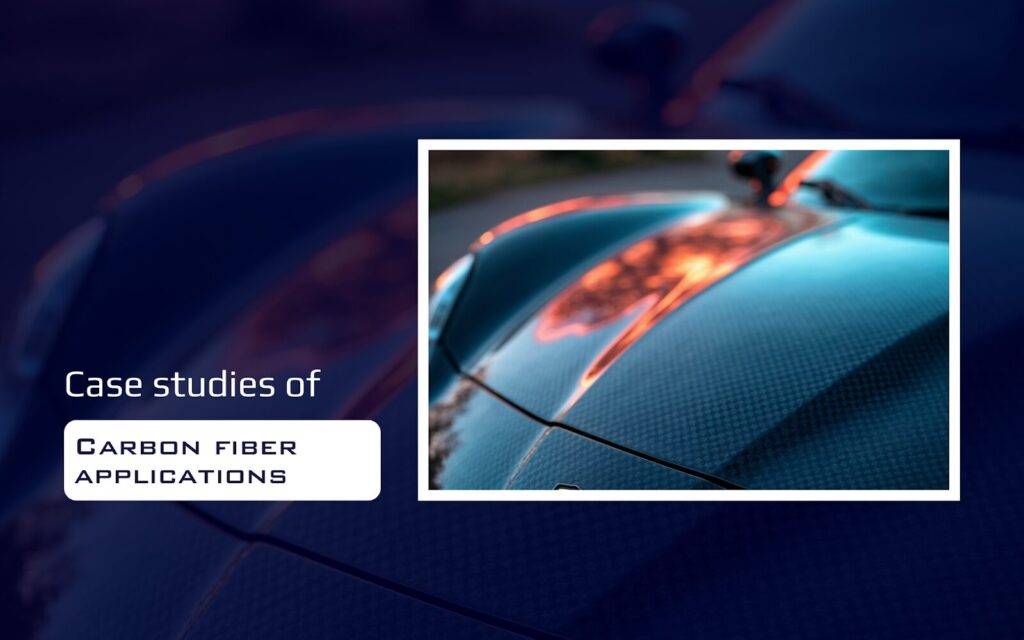
Case Studies of Custom Carbon Fiber Applications
Here are some real-life examples that demonstrate the impact of custom carbon fiber parts in the automotive industry:
1. McLaren 720S: Carbon Fiber Monocoque
The McLaren 720S features a carbon fiber monocoque chassis that combines lightweight construction with exceptional strength.
- Impact: The use of a carbon fiber monocoque reduces overall vehicle weight while providing a rigid structure that enhances handling and crash safety.
- Result: The McLaren 720S achieves a remarkable power-to-weight ratio, contributing to its rapid acceleration and top-tier performance.
2. BMW M4 GTS: Carbon Fiber Hood and Roof
BMW’s M4 GTS uses custom carbon fiber components to enhance both performance and aesthetics.
- Impact: The carbon fiber hood and roof reduce the car’s center of gravity, improving handling and stability at high speeds.
- Result: The weight savings from the carbon fiber components contribute to the M4 GTS’s impressive lap times and dynamic driving experience.
3. Ford GT: Carbon Fiber Wheels
The Ford GT uses custom carbon fiber wheels as part of its performance package, setting it apart from traditional supercars.
- Impact: Carbon fiber wheels reduce unsprung weight, enhancing suspension performance and cornering agility.
- Result: The Ford GT’s carbon fiber wheels contribute to its agile handling and better acceleration, especially on the track.
Conclusion
Custom carbon fiber car parts offer a range of benefits, from weight reduction and enhanced performance to improved safety and durability. With various manufacturing processes available, carbon fiber components can be tailored to fit specific needs, whether for racing, street performance, or aesthetic appeal. As demonstrated by leading automakers, the use of custom carbon fiber parts is not just about performance gains—it’s also a statement of innovation and design.
Interested in upgrading your car with custom carbon fiber parts? Explore our range of options and see how carbon fiber can transform your vehicle’s performance and appearance.