When it comes to enhancing the durability, aesthetics, and performance of metal parts, few surface treatments are as versatile and cost-effective as black oxide coating. Often referred to as blackening or black oxide, this process is widely used across various industries for a host of applications, from aerospace and automotive to precision machinery. If you’re considering black oxide for your next project, this guide will provide an in-depth look at everything you need to know, from the process to the pros and cons, as well as the best practices for ensuring a successful application.
What Is Black Oxide Coating?
Black oxide coating is a conversion coating that forms a thin, black oxide layer on the surface of ferrous materials like steel, stainless steel, copper, and brass. This process involves the chemical conversion of the surface metal into iron oxide, a compound known for its corrosion resistance and aesthetic appeal.
The primary purpose of black oxide is to provide corrosion resistance, while also improving wear resistance, reducing friction, and enhancing the visual appeal of the part. The coating does not increase the dimensions of the part significantly, making it ideal for components where maintaining precise dimensions is crucial.
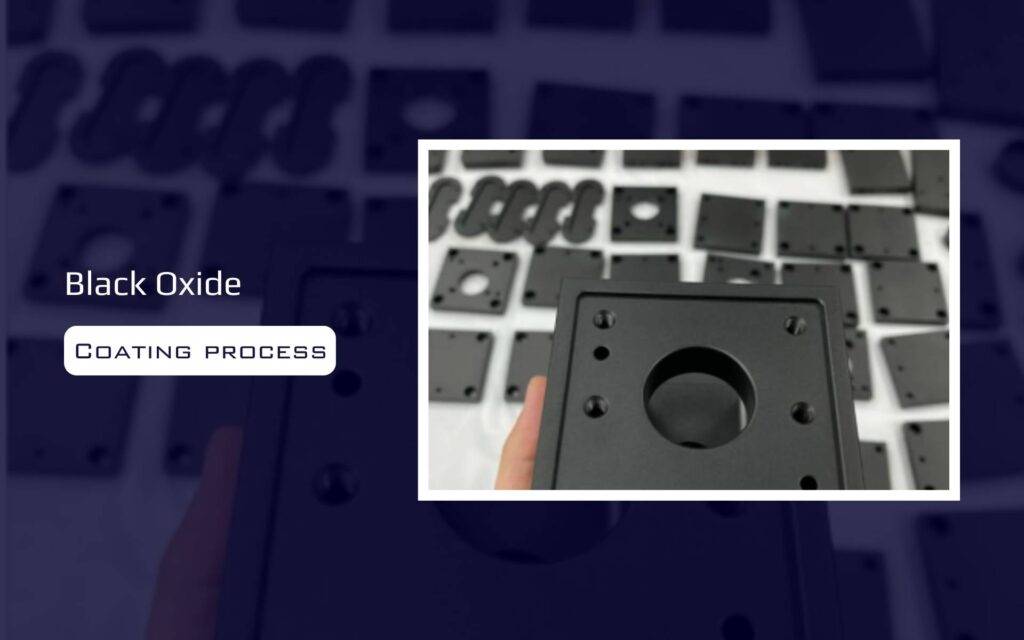
The Black Oxide Coating Process
Achieving a successful black oxide finish requires a precise, multi-step process that involves cleaning, pre-treatment, immersion in a black oxide solution, and post-coating treatments. Here’s a step-by-step breakdown:
1. Cleaning
Before applying the black oxide coating, the metal parts must be thoroughly cleaned to remove contaminants like oil, dirt, and grease. Any debris left on the surface can interfere with the coating process, leading to defects. Common cleaning methods include:
- Degreasing: Removing oils and grease from the metal surface.
- Sandblasting: Using abrasive particles to clean and roughen the surface.
- Chemical cleaning: Using acidic or alkaline solutions to clean the parts.
2. Pre-Treatment
After cleaning, a pre-treatment solution is applied to help the metal surface prepare for the black oxide coating. This may involve:
- Acid baths: Using sulfuric acid or phosphoric acid to etch the surface.
- Phosphate coatings: Applying a thin layer of phosphate to enhance the bond between the metal and the black oxide layer.
3. Black Oxide Coating
The heart of the process involves immersing the cleaned and pre-treated parts into a hot black oxide solution. The solution typically contains a mixture of sodium hydroxide, sodium nitrate, and water, but the exact composition varies depending on the material and desired properties. The immersion time will depend on the metal type and finish requirements. During this stage, the metal surface undergoes a chemical reaction that forms the black oxide coating.
4. Rinsing and Sealing
After the black oxide coating has been applied, the parts are removed from the solution and rinsed thoroughly to remove any excess chemicals. To further protect the coating, the parts are often treated with a sealant or oil. Sealing helps to lock in the protective properties of the black oxide layer, enhancing its durability and resistance to corrosion.
5. Quality Control
Finally, the parts are inspected to ensure that the coating meets all required specifications. This includes checking for uniformity, thickness, adhesion, and corrosion resistance. Quality control measures help identify any defects like discoloration, peeling, or uneven coating.
Types of Black Oxide Finish
There are several types of black oxide finishes, each suited for different applications based on material and performance needs. Here’s a look at the main types:
1. Hot Black Oxide
Hot black oxide is the most common and widely used type. The process involves immersing the metal parts in a high-temperature bath (285°C – 315°C). The salts used in the bath, such as sodium hydroxide and sodium nitrate, help form a durable, thick, and corrosion-resistant black oxide layer. Hot black oxide is commonly used for ferrous metals like steel and iron.
Applications: Aerospace components, automotive parts, military equipment, firearms.
2. Mid-Temperature Black Oxide
Mid-temperature black oxide is a process that operates at lower temperatures than hot black oxide, typically between 120°C and 150°C. This process is used for materials that are sensitive to high heat, such as aluminum and titanium. The resulting finish is typically lighter and less durable but is still effective for corrosion resistance and wear protection.
Applications: Lightweight machinery parts, certain aerospace components, medical equipment.
3. Cold Black Oxide
Cold black oxide is performed at room temperature using a copper sulfate and sulfuric acid solution. It provides a black finish but is less durable than hot black oxide. This type is often used for non-ferrous metals like brass, copper, and zinc.
Applications: Decorative finishes, light industrial components, and parts where the finish’s durability isn’t critical.
Benefits of Black Oxide Coating
Black oxide coating offers several advantages that make it a go-to solution for a wide range of applications. Here are some of the key benefits:
1. Corrosion Resistance
Black oxide provides a layer of protection that significantly enhances the metal’s resistance to corrosion, especially in harsh environments like marine, automotive, and aerospace industries. This makes it an ideal choice for parts exposed to moisture and chemicals.
2. Wear Resistance
The black oxide finish provides a hard surface that resists wear and tear. This is particularly useful in applications where parts are subject to friction, such as automotive components, machinery, and tools.
3. Aesthetics
The dark, matte appearance of the black oxide finish is often desirable in various industries, especially when aesthetics are important. The coating provides a sleek, professional look while also reducing light reflection in applications like medical instruments or firearms.
4. Cost-Effectiveness
Compared to other finishing methods like anodizing or plating, black oxide is relatively inexpensive. It provides an effective solution without the high costs associated with more complex coating processes.
5. Lubricity
The porous nature of the black oxide coating helps to retain lubricants, improving the performance of components that experience friction and wear. This is particularly beneficial in automotive and machinery applications.
Applications of Black Oxide Coating
Black oxide coatings are used in a variety of industries due to their ability to enhance the performance, appearance, and longevity of parts. Here are some common applications:
1. Aerospace
Black oxide is frequently used for aerospace components like screws, bolts, and gears. The coating provides corrosion resistance, making it ideal for parts that will be exposed to extreme temperatures and pressure.
2. Firearms
Firearms, especially parts like barrels and triggers, often use black oxide coating to improve durability and provide a non-reflective surface. This is important in military and tactical applications where stealth and corrosion resistance are critical.
3. Automotive
In the automotive industry, black oxide coatings are applied to engine parts, fasteners, gears, and bearings. The coating helps protect parts from friction and wear, which is essential in high-performance automotive applications.
4. Medical Instruments
Medical instruments, such as surgical tools and diagnostic equipment, often use black oxide finishes to reduce glare and prevent corrosion. The matte finish helps with visibility under bright surgical lights and ensures durability during use.
5. Precision Machinery
Black oxide coatings are commonly used on gears, shafts, and bearings in precision machinery. These components need to be able to withstand high levels of friction and wear while maintaining their structural integrity. Black oxide provides a cost-effective solution for these demanding applications.
Considerations for Using Black Oxide Finish
While black oxide is a versatile and effective finish, there are several factors to consider when choosing this coating for your parts:
1. Material Compatibility
Black oxide works best with ferrous materials such as steel, stainless steel, and copper. However, its application on non-ferrous metals like aluminum and titanium is more limited. Ensure that the material you’re working with is compatible with black oxide to achieve the best results.
2. Intended Use
The intended application of the parts will play a significant role in deciding whether black oxide is the best finish. For example, parts exposed to harsh environmental conditions or requiring high wear resistance will benefit from black oxide, while parts requiring high aesthetic standards may need an alternative finish.
3. Durability
While black oxide provides excellent corrosion resistance, it is not as durable as other finishes like anodizing or plating. It may require periodic maintenance, particularly in high-stress or outdoor environments.
4. Appearance
Black oxide finishes are typically matte and provide a sleek, non-reflective appearance. If a shiny or glossy finish is required, other coatings may be more appropriate. However, black oxide is ideal when the goal is to reduce glare and improve the overall appearance of industrial components.
5. Thickness Control
The thickness of the black oxide coating can vary depending on factors such as the material type and immersion time. While the increase in thickness is minimal, it’s important to ensure consistency across all parts, especially when precision is key.
Common Defects in Black Oxide Coating and How to Solve Them
Despite its advantages, the black oxide coating process can sometimes result in defects. Here are a few common issues and how to solve them:
1. Uneven Coating
This typically occurs when the parts are not cleaned or prepared properly before the coating process. Ensure that the parts are thoroughly cleaned and that the coating thickness is monitored during the process.
2. Discoloration
Improper rinsing or contaminated rinse water can lead to discoloration of the coated parts. Make sure the parts are rinsed thoroughly with clean water to remove any excess chemicals.
3. Blotchy Appearance
A blotchy appearance can be caused by improper agitation during the coating process. Ensure that the parts are agitated properly in the solution to ensure an even coating.
4. Peeling or Flaking
This issue may arise if the parts are not cleaned properly or if the coating is applied too thickly. Thorough cleaning and careful monitoring of the coating thickness can help avoid this issue.
Conclusion
Black oxide coating is a versatile, cost-effective surface finish that provides corrosion resistance, wear resistance, and an aesthetically pleasing appearance. It is widely used across industries like aerospace, automotive, and medical instruments. However, it’s important to consider material compatibility, intended use, durability, and other factors when selecting this finish for your parts.
If you’re looking for a durable and affordable coating option for your precision machined parts, black oxide may be the perfect choice. Be sure to work with experienced professionals who understand the intricacies of the process to achieve the best results.