Anodized gold and steel surface finishing have become essential for improving the functionality and appearance of metal components. This article delves into the latest advancements in anodizing techniques, exploring how they enhance both aesthetics and durability, making them indispensable in many modern industries.
Introduction to Anodized Gold and Steel
Anodized gold and steel undergo a sophisticated electrochemical process designed to enhance their surface properties. Anodizing involves immersing the metal in an acid electrolyte bath, where an electrical current is passed through, creating a thick, protective oxide layer. This process improves the metal’s resistance to corrosion, wear, and other environmental factors, making it a preferred choice for both industrial and decorative purposes.
Anodized coatings can be produced in various colors and finishes, including vibrant gold hues that stand out aesthetically. This process not only provides a decorative finish but also significantly increases the material’s lifespan and performance, offering protection that goes beyond conventional surface treatments.
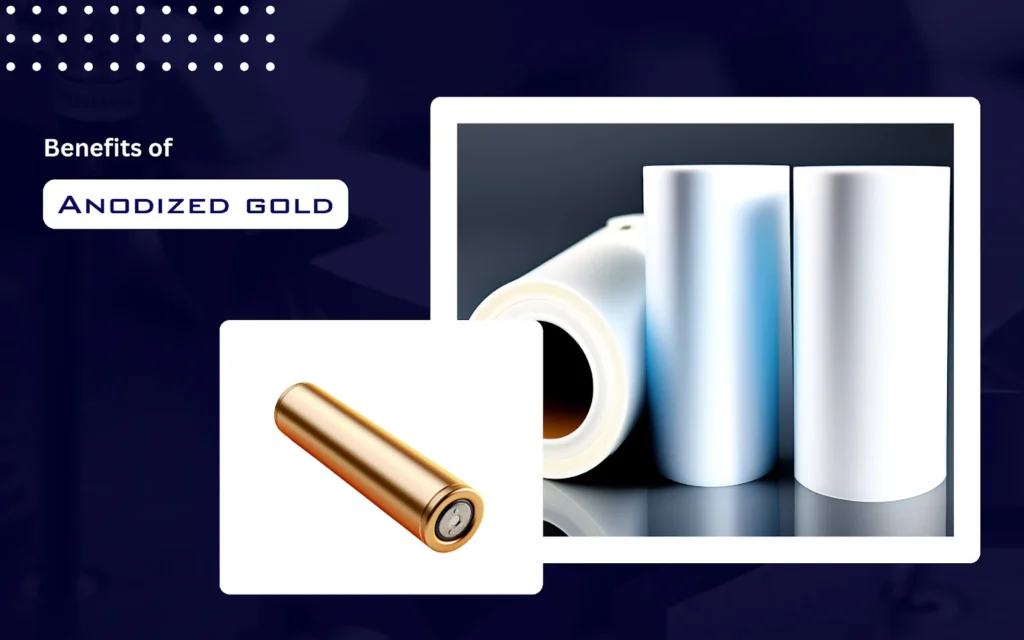
- Enhanced Durability: Anodized surfaces possess high resistance to abrasion, corrosion, and wear, extending the lifespan of the metal components.
- Improved Aesthetics: Anodizing allows for a range of color options, including anodized gold, which can enhance the visual appeal of products and components.
- Increased Hardness: The anodized layer is much harder than the base metal, offering superior scratch and dent resistance.
- Environmentally Friendly: Anodizing is a non-toxic process that produces no hazardous by-products, making it an eco-friendly choice for surface finishing.
Innovative Techniques in Anodizing
Anodized gold and steel can be processed using several advanced techniques, each offering specific advantages:
1. Type I Anodizing
Type I anodizing employs a chromic acid bath to produce a thin but highly durable coating. It is ideal for applications requiring minimal thickness and high resistance to corrosion and chemicals.
2. Type II Anodizing
Type II anodizing, using sulfuric acid, creates a thicker and more porous oxide layer. This method is popular for its excellent color versatility, including the ability to achieve various shades of anodized gold.
3. Type III Anodizing
Type III, or hard anodizing, results in a very thick and dense coating. This method is suited for applications where extreme durability and resistance to wear are essential. It is commonly used in aerospace and military applications.
4. Chemical Film/Alodine
Chemical film, also known as Alodine, provides a protective coating that offers corrosion resistance while maintaining electrical conductivity. It is frequently used in aerospace and defense sectors due to its lightweight and protective qualities.
Applications of Anodized Gold and Steel
Anodized gold and steel find applications across various industries, thanks to their enhanced properties:
- Electronics: Anodized gold is used in electronics for connectors and other components, where its conductivity and aesthetic appeal are crucial.
- Aerospace: Hard anodized components are essential in aerospace for their durability and resistance to harsh conditions.
- Automotive: Anodized steel parts are used in automotive applications to improve both performance and appearance.
- Architecture: Decorative anodized gold is popular in architectural features, providing both visual appeal and protection.
Choosing the Right Anodizing Technique
Selecting the right anodizing technique depends on the specific requirements of your application:
- Desired Coating Thickness: Determine whether you need a thin, decorative coating (Type I) or a thick, protective layer (Type III).
- Environmental Conditions: For extreme environments, Type III anodizing is preferred, while Type II offers flexibility in color and thickness.
- Electrical Conductivity: If conductivity is important, Chemical Film/Alodine is the best choice.
Conclusion
Anodized gold and steel surface finishing techniques offer numerous benefits, from enhanced durability to improved aesthetics. Understanding the various anodizing methods and their applications allows you to select the most suitable technique for your needs. ProtoTech Machining provides advanced anodizing solutions to meet a wide range of industry requirements.