Introduction
Alodine, a term that’s widely recognized in the world of manufacturing and precision machining, refers to a surface treatment process that involves the application of a chromate conversion coating. This finish has become a crucial step in enhancing the performance and durability of metal parts, especially those that are subjected to harsh environments. Whether you’re working with aluminum alloys or other metals, understanding the alodine finish process is key to ensuring that your parts meet the required standards of corrosion resistance, aesthetics, and functionality.
This comprehensive guide will provide you with everything you need to know about Alodine—what it is, why it’s essential for precision-machined parts, how the coating process works, and how it compares to other finishing methods such as anodizing. By the end of this post, you’ll have a solid understanding of why Alodine is a go-to choice for many industries and applications.
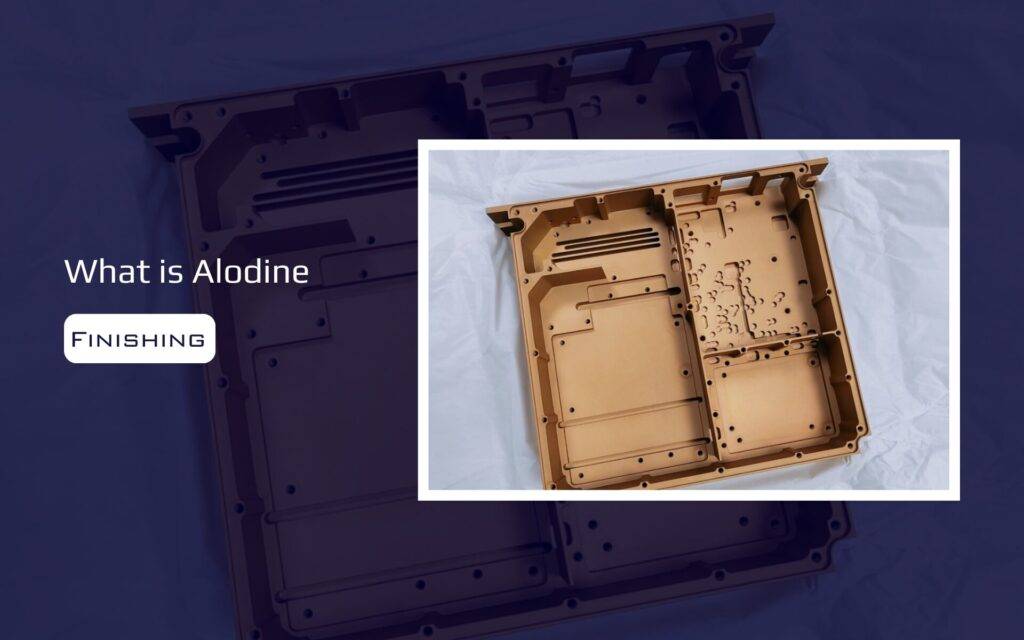
What is Alodine Finishing?
Alodine, also known as chromate conversion coating or Chem Film, is a surface treatment used primarily on aluminum alloys. The primary purpose of Alodine finish is to protect the metal surface from corrosion, while also offering other benefits such as enhancing electrical conductivity, improving paint adhesion, and increasing the metal’s aesthetic appeal. Unlike other coatings, Alodine finishes are thin and do not alter the mechanical properties of the metal, such as strength and weight.
The Alodine coating is applied through a chemical reaction where the metal is exposed to a solution containing chromates. This process forms a protective layer on the metal’s surface, which serves as a barrier against environmental factors like moisture, salt, and chemicals, thereby increasing the lifespan of the metal parts.
Why Alodine Finish is Essential for Precision-Machined Parts
1. Enhancing Corrosion Resistance
Corrosion is one of the biggest challenges that metals face, especially when exposed to harsh environmental conditions such as saltwater, high humidity, or industrial chemicals. For precision-machined parts, corrosion can significantly degrade performance, leading to failure and increased maintenance costs. Alodine finish is highly effective at preventing such issues, especially for aluminum alloys, which are prone to corrosion when left unprotected. By forming a thin, but durable, coating, Alodine helps protect the underlying metal, ensuring that parts remain functional and intact for longer periods.
2. Promoting Paint and Primer Adhesion
In many industries, metal parts need to be painted or primed for aesthetic purposes or to provide additional protection. Alodine provides an excellent base for paint adhesion by forming a chemically bonded surface that ensures the paint or primer sticks better to the metal. This is particularly beneficial in aerospace and automotive industries, where high-quality finishes are essential. The improved adhesion also reduces the risk of peeling, chipping, or flaking of the paint, ensuring that the parts maintain their appearance over time.
3. Maintaining Electrical Conductivity
For certain applications, particularly in the aerospace and electronics industries, it is important that metal parts maintain their electrical conductivity. Alodine finishes are unique because they balance the need for corrosion resistance with the requirement for electrical conductivity. The finish allows the metal to maintain its electrical properties while still benefiting from the protective qualities of the coating. This makes Alodine a versatile choice for parts that need to function effectively in both conductive and corrosive environments.
The Science Behind Alodine Coating
The Alodine coating process relies on a chemical reaction between the metal and a chromate solution. This process is commonly referred to as chromate conversion coating. When the metal part is submerged in the chromate solution, it reacts with hydroxide ions and trivalent chromium to form a protective oxide layer on the surface.
The coating layer is a complex metal-chromium molecule, which forms a continuous gelatinous film on the surface. The result is a thin, yet highly effective, protective layer that prevents further oxidation or damage to the metal. Importantly, Alodine is distinct from anodizing because it does not involve an electrical current; instead, it is a simple chemical process that creates a passivating oxide film on the surface.
Types of Alodine Finishes and Their Significance
Alodine finishes come in a variety of types, each with specific applications and benefits. The most commonly used types are MIL-DTL-5541 Type I and Type II, which are part of the U.S. military and aerospace standards for chromate conversion coatings. Let’s dive into the details of these types:
1. MIL-DTL-5541 Type I (Hexavalent Chromium)
Type I Alodine finishes use hexavalent chromium as a primary component. These coatings provide excellent corrosion resistance and are commonly used in aerospace, military, and defense applications. However, due to the hazardous nature of hexavalent chromium, the use of Type I coatings has been restricted in recent years. It’s still widely used for parts that require maximum corrosion resistance and are less concerned with the environmental impact.
2. MIL-DTL-5541 Type II (Trivalent Chromium)
Type II Alodine coatings are a safer alternative to Type I coatings, using trivalent chromium instead of hexavalent chromium. The result is a coating that is still highly effective at preventing corrosion but with a much lower environmental impact. Type II coatings are generally colorless and are favored in the aerospace and precision machining industries due to their lower toxicity and better safety profile. This type of Alodine finish is currently the most commonly used for aluminum alloys.
3. Other Alodine Types
Apart from MIL-DTL-5541 Type I and Type II, there are other Alodine finishes like AMS-2473, AMS-C-5541, and others. These variations are often used for specific applications where other properties like better conductivity or aesthetics are required. For example, AMS-2474 is a more robust finish, designed for components exposed to extreme conditions.
The Alodine Coating Process: Step-by-Step
Applying an Alodine coating involves several steps, ensuring that the metal parts are cleaned, prepared, and coated properly for optimal results. Below is a step-by-step guide to applying the Alodine finish:
Step 1: Cleaning the Metal Part
Before any coating is applied, the metal part must be thoroughly cleaned to remove dirt, grease, and contaminants. Common cleaning agents like Alumiprep 33 are used to degrease and prepare the surface for the coating process. This step ensures that the Alodine finish adheres properly to the metal.
Step 2: Etching the Product
Etching the metal surface is crucial as it prepares the areas where the Alodine coating will be applied. It prevents the coating from adhering to certain parts of the metal, which may need to remain free of the finish.
Step 3: Deoxidizing
Deoxidizing removes any oxides or other contaminations from the surface, ensuring that the Alodine finish forms a uniform and effective protective layer. This step is important to achieve optimal corrosion resistance.
Step 4: Applying the Alodine Coating
The metal part is submerged in the Alodine solution, where the chemical conversion coating is applied. This can also be done through spraying or brushing, depending on the requirements. The coating process lasts for a set time, depending on the desired thickness.
Step 5: Final Wash and Drying
After the Alodine finish has been applied, the metal part is rinsed and dried. It’s important to remove any excess solution to ensure the coating is clean and uniform. The final product is then left to dry fully before use.
Alodine vs. Anodizing
When comparing Alodine to anodizing, there are notable differences in terms of process, impact on dimensions, functionality, and cost.
Process
Anodizing involves an electrochemical process where the metal is subjected to an electrolytic bath, causing it to form a protective oxide layer. Alodine, on the other hand, is a chemical conversion coating that does not require an electrical current.
Impact on Dimensions
Anodizing adds a thicker oxide layer to the surface of the metal, which can slightly alter its dimensions. Alodine, however, creates a much thinner film, meaning the final dimensions of the metal parts are less affected.
Functionality
While both Alodine and anodizing provide corrosion resistance, anodizing is often preferred for its decorative qualities and thicker, more durable finish. Alodine, however, is better for applications where maintaining electrical conductivity is critical, as it has less impact on the metal’s conductive properties.
Cost
Alodine is generally more cost-effective than anodizing due to its simpler and quicker application process. Anodizing, because it involves an electrochemical bath, tends to be more expensive.
Key Advantages and Disadvantages of Alodine Finish
Advantages:
- Straightforward Process: The Alodine application process is simple and can be done quickly without the need for expensive equipment.
- Corrosion Resistance: Provides excellent corrosion resistance, particularly for aluminum alloys.
- Improved Paint Adhesion: Acts as an ideal base for paint and primer adhesion, especially in aerospace and automotive industries.
- Electrical Conductivity: Does not compromise the electrical properties of aluminum, making it suitable for electrical components.
Disadvantages:
- Thin Finish: Alodine is less durable than other finishes like anodizing and may not provide adequate protection in high-abrasion environments.
- Toxicity: The chromate solution used in Alodine coatings can be toxic, and proper handling and disposal are required.
- Limited Color Options: Unlike anodizing, which offers a broad range of colors, Alodine provides only clear or golden finishes.
Industry Applications of Alodine Finish
Alodine coatings are used in a variety of industries where corrosion resistance and surface protection are critical. Some common applications include:
- Aerospace: Alodine is frequently used to protect aluminum parts in aircraft, including fuselages, landing gear, and wing components.
- Military and Defense: Parts used in military vehicles, weapons, and marine equipment are often coated with Alodine for enhanced durability and corrosion resistance.
- CNC Precision Machining: Alodine is widely used in CNC machining to provide a corrosion-resistant finish without affecting the part’s dimensional accuracy.
Conclusion
Alodine finishes play a crucial role in ensuring that precision-machined parts maintain their integrity, functionality, and appearance over time. Whether for aerospace, military, or other high-performance industries, the Alodine chemical conversion coating is a go-to solution for enhancing metal parts, especially aluminum alloys. By understanding the process, types, and applications of Alodine, manufacturers can ensure that their products perform at their best in even the harshest conditions.