Introduction to Additive vs. Subtractive Manufacturing
In the ever-evolving world of manufacturing, two dominant methods stand out for low-volume production: additive manufacturing and subtractive manufacturing. Both techniques have their own unique advantages and are suited for different applications. This guide delves into additive vs. subtractive manufacturing, exploring their differences and how each method influences low-volume production.
Understanding Additive Manufacturing
Additive manufacturing, often referred to as 3D printing, is a process where components are built layer by layer. This technique is renowned for its ability to produce complex geometries and intricate prototypes. It has gained popularity among companies seeking flexibility and reduced lead times, particularly in low-volume production scenarios.
Types of Additive Manufacturing:
- Fused Deposition Modeling (FDM): This is the most widely used method for creating plastic parts. It involves extruding melted plastic through a nozzle to build up the part layer by layer. FDM is favored for its affordability and ease of use, making it ideal for prototyping and small-batch production.
- Stereolithography (SLA): SLA is known for its high-resolution capabilities, which are perfect for creating detailed prototypes. This method uses a laser to cure liquid resin into solid parts, achieving a smooth surface finish and high accuracy.
- Selective Laser Sintering (SLS): This technique works with both plastics and metals. It uses a laser to sinter powdered material, which then forms a solid structure. SLS is advantageous for producing parts with complex geometries and for functional prototypes.
Understanding Subtractive Manufacturing
Subtractive manufacturing involves removing material from a solid block using various machining techniques. Although more traditional than additive methods, subtractive manufacturing remains vital for producing precise and durable parts. This method is especially useful for applications requiring high strength and durability.
Common Subtractive Methods:
- CNC Milling: This technique is ideal for cutting complex shapes and features from a block of material. CNC milling machines can create intricate details and precise dimensions, making it suitable for both prototyping and final production.
- CNC Turning: Used primarily for creating cylindrical parts, CNC turning involves rotating the material while a cutting tool removes excess material. This method is essential for producing parts with symmetrical shapes and high precision.
- Laser Cutting: Perfect for sheet metal applications, laser cutting uses a high-powered laser to cut or engrave material. It offers excellent accuracy and is ideal for creating detailed designs and clean edges.
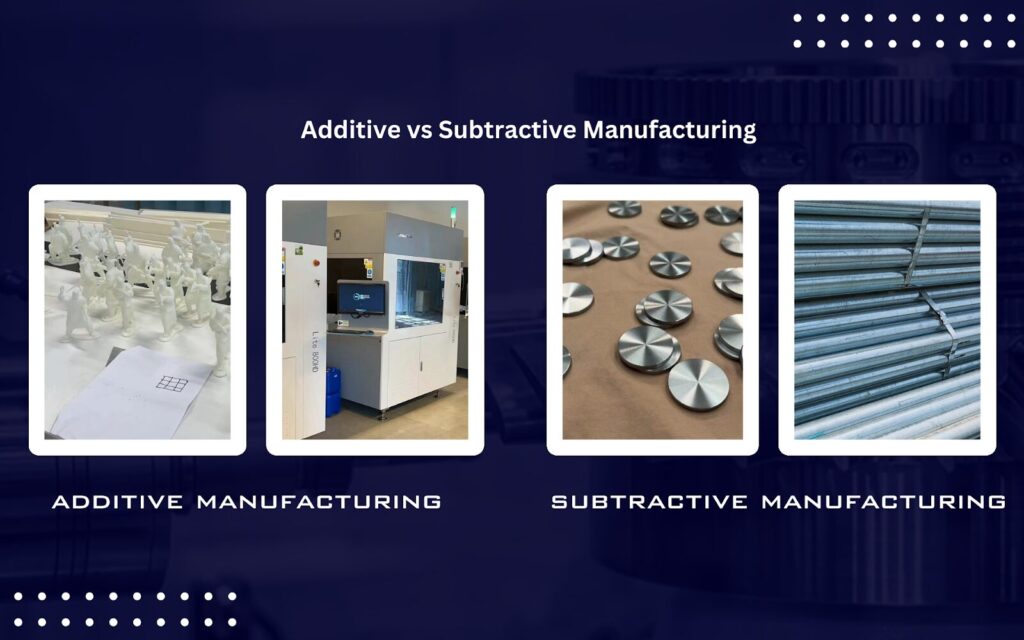
Comparing Additive vs. Subtractive Manufacturing for Low-Volume Production
When evaluating additive vs. subtractive manufacturing, several factors come into play, including cost, speed, and material options.
- Cost: Additive manufacturing generally proves to be more cost-effective for complex parts and prototypes due to its lower material wastage and reduced setup costs. Conversely, subtractive manufacturing can be more economical for simpler designs where the cost of tooling and setup is justified by the part’s durability and precision.
- Material Flexibility: Additive manufacturing offers a wide range of material options, including various plastics, metals, and composites. This flexibility allows for experimentation with different materials to achieve the desired properties. Subtractive manufacturing, while more limited in material choices, allows for a broader range of finishes and often uses materials with higher strength and durability.
- Lead Time: Additive manufacturing is capable of producing parts within days, thanks to its quick setup and production processes. Subtractive manufacturing, however, may involve longer lead times due to the complexity of setup and machining processes.
Key Factors to Consider When Choosing a Method
Choosing between additive vs. subtractive manufacturing involves evaluating several critical factors, especially for low-volume production:
- Complexity of Design: Additive manufacturing excels in producing complex and intricate parts that may be challenging to achieve with traditional subtractive methods. If your design includes intricate details or geometric complexity, additive manufacturing could be the preferred choice.
- Material Requirements: For applications requiring high-strength and durable materials, subtractive manufacturing might be the better option. This method can handle a wider range of robust materials and deliver parts with superior mechanical properties.
- Surface Finishing: Subtractive manufacturing often provides better surface finishes and precision, making it suitable for applications where appearance and exact specifications are crucial.
- Budget Constraints: Additive manufacturing can significantly reduce upfront costs, particularly when producing prototypes or small batches. Its ability to eliminate tooling costs makes it an attractive option for budget-conscious projects.
- Production Speed: Additive manufacturing generally offers faster production cycles for prototypes and low-volume runs. Its rapid setup and production capabilities can accelerate project timelines.
Conclusion
Choosing the right manufacturing method between additive and subtractive manufacturing depends on your specific project requirements. If your project demands intricate designs and quick turnaround times, additive manufacturing might be the best choice. However, for high precision and durability, subtractive manufacturing is likely the more suitable option. Often, combining both methods can provide the best balance of efficiency, cost, and quality, ensuring optimal results for your low-volume manufacturing needs. Understanding the strengths and limitations of each technique is crucial for making an informed decision that aligns with your production goals.