Quality Assurance
Uncompromising Quality Assurance
Each time materials enter our warehouse, they undergo thorough spectroscopic analysis to ensure their precise composition and characteristics. To provide you with complete confidence in the parts you receive, we include mill certs and testing reports with every shipment.
We offer a 100% full refund policy.
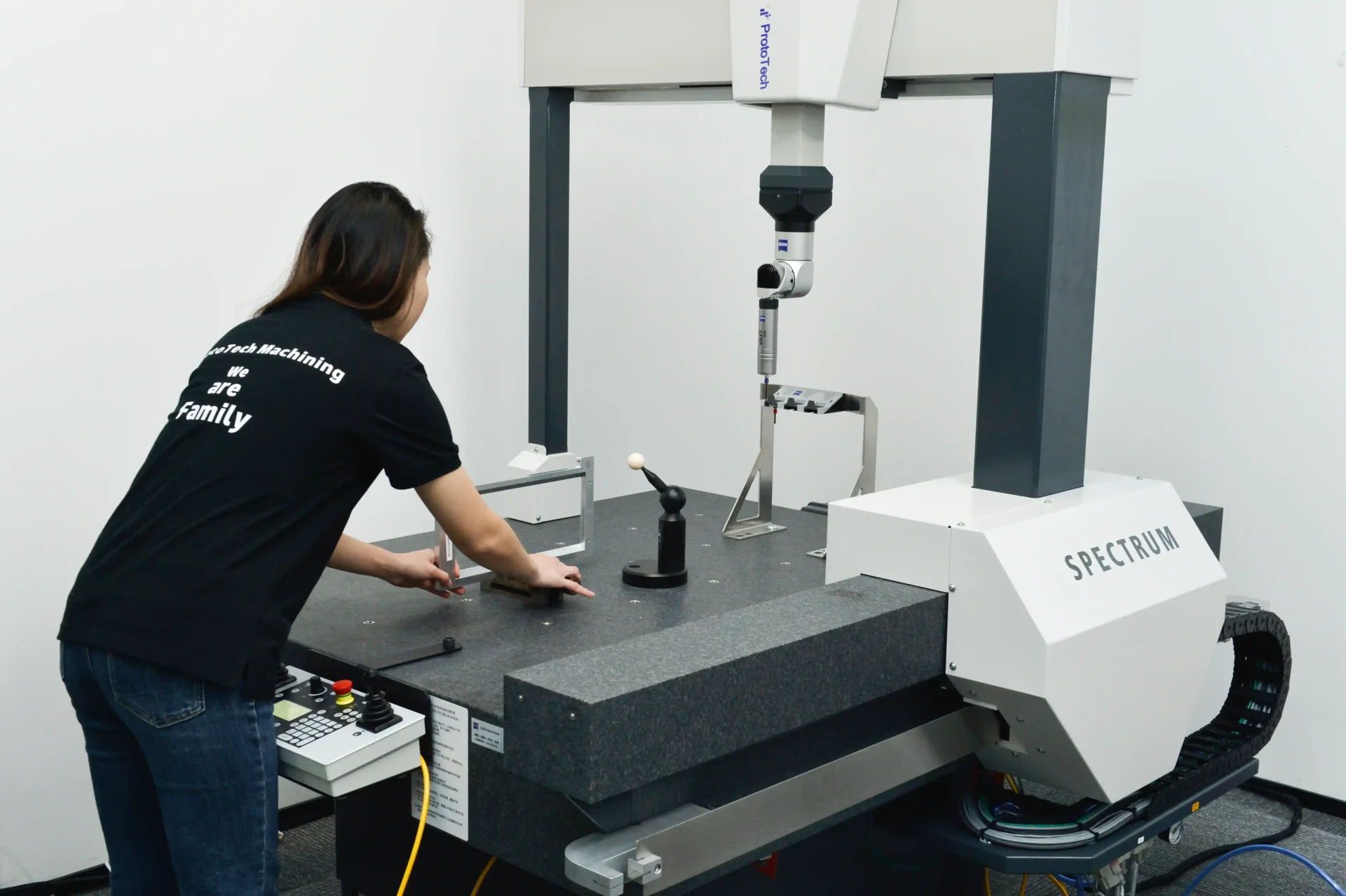
Our quality process is run through the whole projects from RFQs to production shipment.
Two independent reviews of the purchase order is where our QA begins, determining that there are no questions or conflicts regarding dimensions, material, quantities, or delivery dates.
Then reviewed by experienced personnel involved in the set up and production and individual inspection reports are made for each operation that is required to produce the part.
All special quality needs and instructions are documented and inspection intervals are then assigned based on tolerances, quantities or complexity of the part.
We minimize risk by tracking and analyzing every step of our manufacturing process to minimize part to part variation, and assure consistent, reliable quality for every part, every time.
Quality Control is Our Number one Priority for All CNC Precision Machining Products
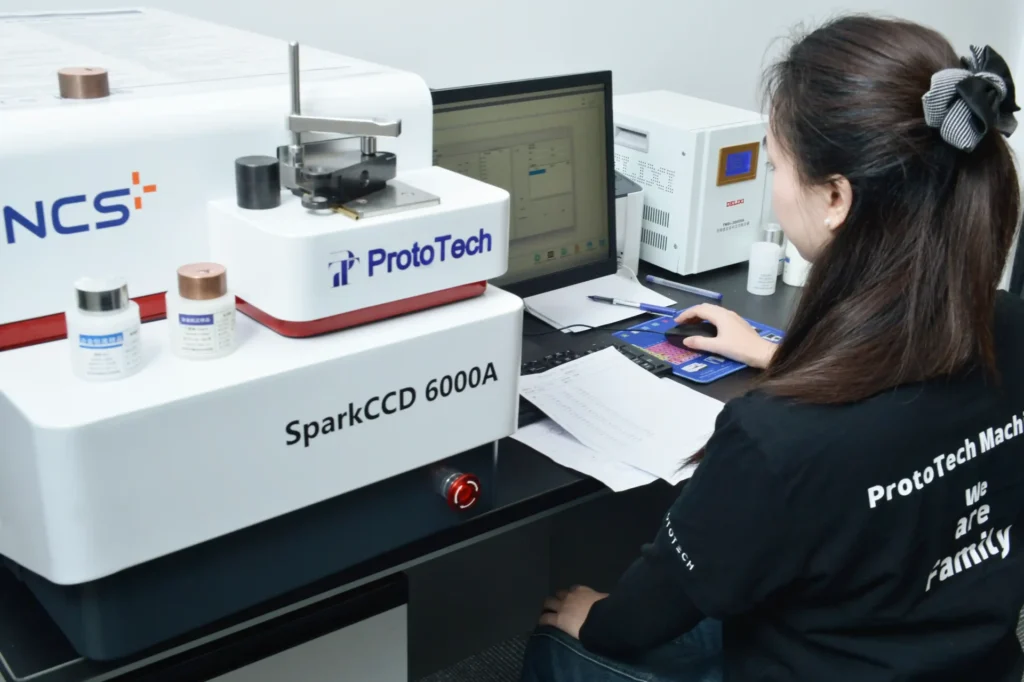
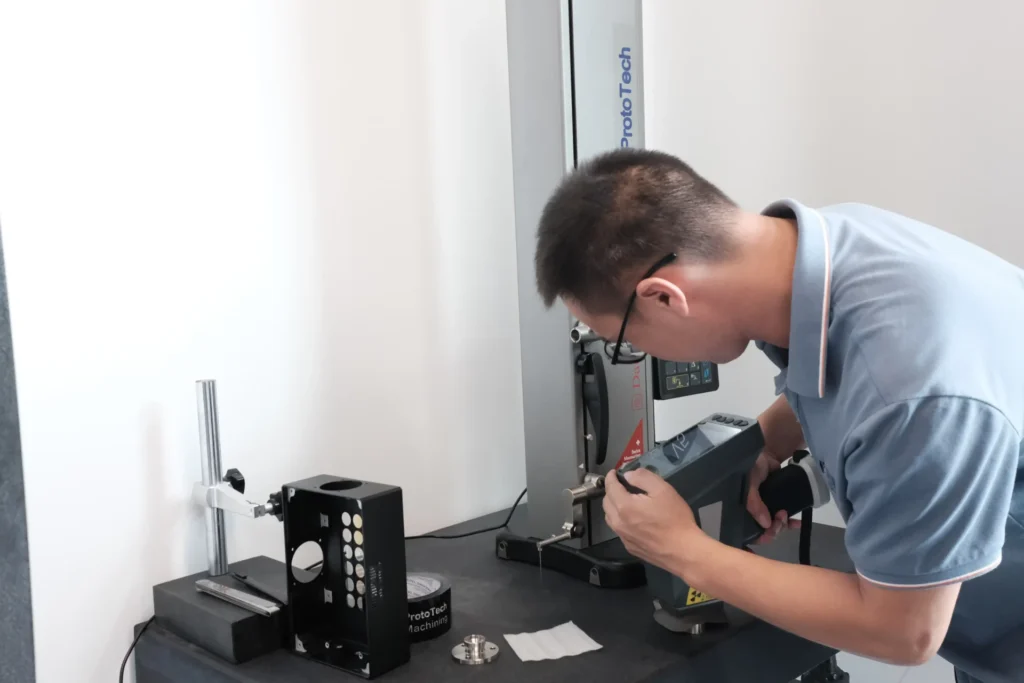
Incremental Processes Ensuring Quality
Uploading
Customer Communication
Designing
Products and Services
Manufacuring
Verification of Purchased Products
Shipping
In-Process Inspections
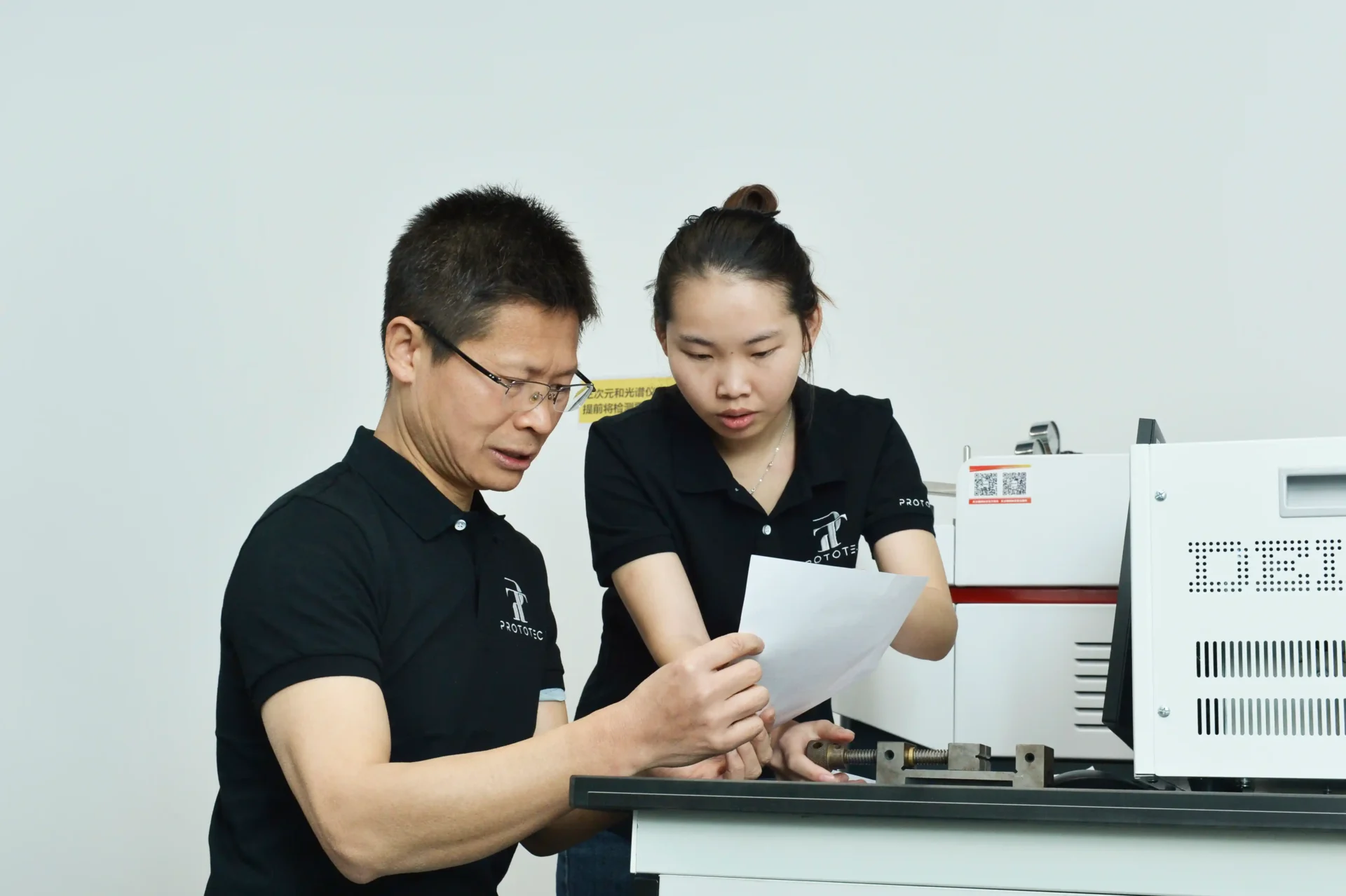
Final Acceptance Inspection
Completed CNC machining services yield products that undergo the concluding QC scrutiny. Initially, inspectors ensure the execution of all predefined and ongoing examinations. Following this, they conduct the remaining assessments, employing a Coordinate Measuring Machine (CMM) as needed, to validate product conformity.
Our quality management system’s consistency and proficiency are evaluated by internal audits, measuring quality performance, and gauging customer satisfaction.
Quality engineers handle the verification of product specs and technical details for incoming materials, ensuring they align with drawing, customer-end application requirements, and technical specifications. All initial verifications, like CNC machining services, 3D printing, and aluminum casting molds, must be met for the procured materials. After certification, the quality team confirms that materials, possibly involving carbon fiber manufacturing or sheet metal fabrication, are inspected and meet supplier-end standards.